Grinding rivet gun nose-pieces flat
Following TAF advice I machined the Sunex SX0918T nose-pieces to be flat. Before doing this I verified the possibility of replacement in the event of a botched job. Support for this rivet gun outside the US is non-existent, however I was able to find a US retailer (Jagor equipment) who was willing to source and ship the following to Australia. I have ordered these for general backup.
2 x RS612303 Jaw "M"
1 x RS612703 nose piece 3/32" (2.4mm)
1 x RS612704 nose piece 1/8" (3.2mm)
1 x RS612705 nose piece 5/32" (4.0mm)
1 x RS612706 nose piece 3/16" (4.8mm)
I confirmed the Sunex SX0918T nose-pieces have a UNF 3/8" 24 thread. I tack welded a UNF 3/8" 24 to a 1/4" steel plate, laying precisely flat on the surface. Using a dremel flat surface grinding stone in a drill press, with cutting oil I was able to precisely grind away the dishing on the 4.8mm, 4mm, and 3.2mm nose-pieces. I then smoothed with 800-grit sandpaper wet, then 1200 grit. I finished off with a 800grit Grey Vlies, which left a dull polish.
I then tested the newly ground nosepieces with the Gesipa rivets as before. The accuracy of the grind was confirmed by the improved, yet uniform contact between the rivet head and the aluminium surface. The contact was improved greatly, with the region of contact for the 4.8mm rivets in particular becoming a uniform broad ring extending well in from the edge of the rivet. This is a large improvement from the previous rivet behaviour. Aside from plausible mechanical improvement, this points to a far smaller cavity under the rivet head to trap Duralac, when used. The dishing of the 4mm rivet near the shaft, while not reduced to zero, is also considerably reduced, with fairly uniform contact.
I presume the fact that the flat nose-piece also bring a much greater force to bear near the centre of the rivet, given that the gap under the rivet head is almost completely closed. This might lead to a greater deformation of the shaft of the rivet - with possible consequent expansion - just under the surface of the rivet head. It is reasonable to suppose the flat-head leads to a tighter setting of the rivet. This will guide my decision-making with regards to the existing rivets in the build.
It is hard to tell just how improved the rivet setting is, in the absence of strength testing equipment.
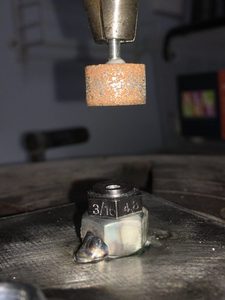
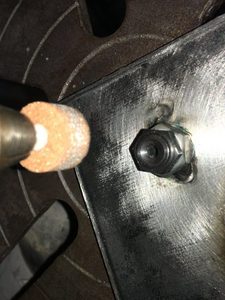
4.8mm before starting
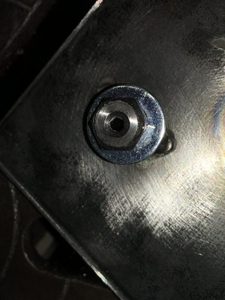
4.8mm using dish to verify levelness of grind
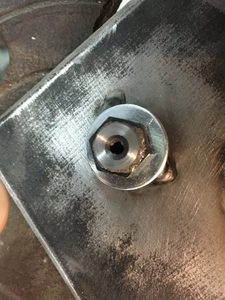
4.8mm further into grind
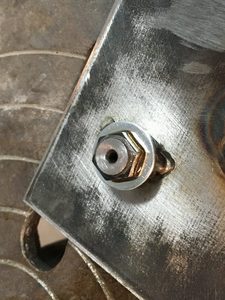
4.8mm finished grind
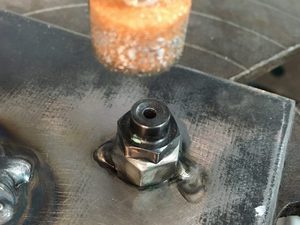
4mm before starting
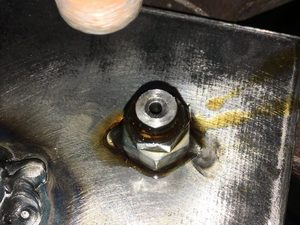
4mm partly ground
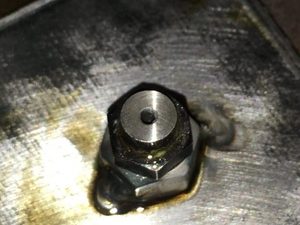
4mm finished grind
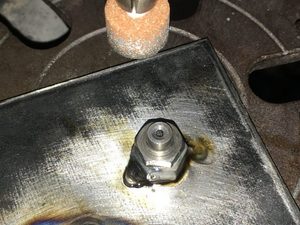
3.2mm before grinding
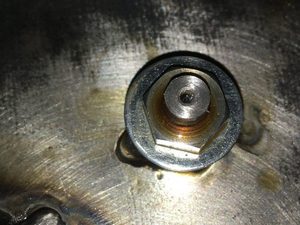
3.2mm partly ground
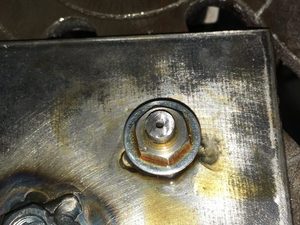
3.2mm finished grind
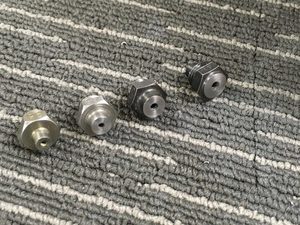
After polishing (2.4mm not altered)
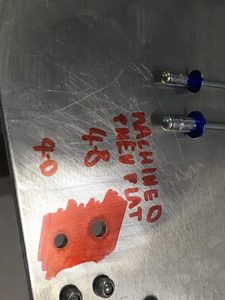
Testing 4.8mm and 4mm head contact
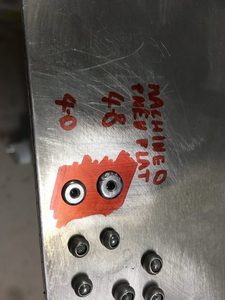
Testing 4.8mm and 4mm head contact: setting with ground flat heads
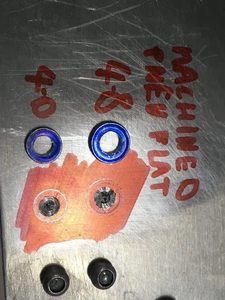
Testing 4.8mm and 4mm head contact: underside head contact
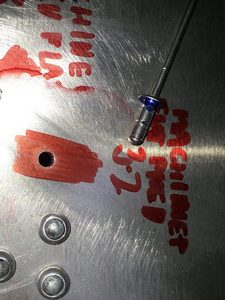
Testing 3.2mm head contact
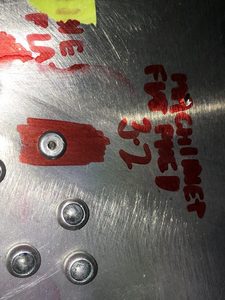
Testing 3.2mm head contact: after setting with ground flat heads
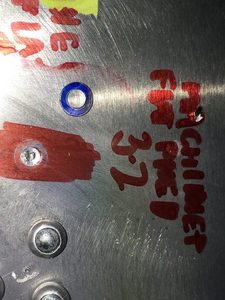
Testing 3.2mm head contact: underside head contact

4.8mm closeup
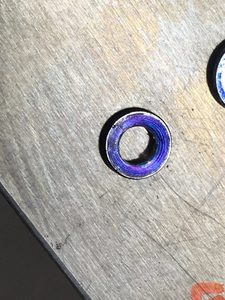
4mm closeup
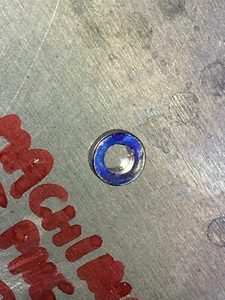
3.2mm closeup
This post is from Adam Dickson