Upsizing LH and RH wing main spar topside holes between ribs 7 and 8
After extensive investigation, it was concluded that the RH leading edge did indeed have a walkoff with the main spar holes. Skin 1 match the main spar perfectly. By twisting the wing slightly it was possible to match these leading edge holes but to do so was found to freeze this twist in place and result in horrendous oil canning of skin 4 when it was subsequently fitted. It was concluded that a leading edge hole mismatch must be worked with. I did not want to request a replacement due to delays, the costs involved in reducing those delays by air-freight, and the fact that Sling have already assisted me enormously with providing some replacement parts - customised fuel tank skins in particular as well as some other skins - to solve far more serious tolerance issues in more critical parts of the wing.
How bad is the mismatch? The mismatch was very small rib 8 but grew to approx 1.7mm at rib 7. If I were to upsize and recentre to 4.8mm I could absorb this mismatch for all but the last 5 or so leading edge skin rivets, and the residual elongation would be about 1mm at worst. Important to note that the really important structural connection, that of skin 4 to the main spar was unaffected. Also important to note that the 2D rule would continue to be satisfies for all skins after this upsizing. Further the main spar flange hole centre to edge distance satisfies this guideline by a huge margin.
Another factor leading me to the conclusion that the walkoff was genuine was that I was able to fit the fuel tank skins to achieve a perfect match not only with the top an bottom spar flanges but also achieve a snug fit with the leading edge skin with perfect registration with its 3.2mm rivet holes. Even after this, the mismatch with the main spar holes remained. If I had tried to force the leading edge, the mismatch with the fuel tank skin would have been severe. I which I had checked this earlier as I would have avoided much investigation time. In the event, no wrong turns were made and I did not stuff up any skins or main spars. Also, the slight adjustments of the leading edge ribs (documented in other posts) would have still been substantially necessary, as they were very tight under the leading edge skin with enough mismatch to require some forcing. Note that part of the original motivation for adjusting the leading edge ribs slightly was to hopefully make the leading edge skin "wrap" slightly differently to reduce the mismatch. Indeed, if I installed the leading edge with the leading edge ribs removed (more time and work!) I could substantially reduce to mismatch to a low level. But this was a chimera as it turned out, for the fuel tank test fit eventually told the true story.
Just as well I did not get too aggressive and took a bit of a break between observations to organise my approach.
So I went ahead and did the upsizing and recentering. I really did want to avoid doing this, particularly on the upper leading edge. The slightly higher profile of the 4.8mm rivets might have a very slightly higher drag. This in turn might affect the precise instant at which this part of the wing stalls in a landing as the wing progressively stalls from root to tip (due to washout). These thoughts lead me to the conclusion that I should upsize the corresponding rivets on the LH wing. In fact the LH wing leading edge does not have this mismatch to nearly the same degree, but careful examination did confirm some cleaning and hole elongation would also be required, particularly near rib 8. So this observation made it easier to make the decision to follow this upsizing approach for both wings, and be done with it!
To do: add a photo showing the worst-case elongation of the RH leading edge skin hole (about 1mm) near rib 7. This degree of elongation is actually just within the elongation which is accepted by Sling in production for 4mm holes. My impression is that such mismatches are not uncommon, and are routinely cleaned out and "hidden" under rivets. In a sense my build, in its efforts to eliminate this scenario wherever possible, is attaining a build standard in excess of a reasonable production minima. To date the only locations where elongation is present in the build (empennage and wings) is in the following locations:
The top and bottom-most 4mm rivets on ribs 2, 3, and 4 where they connect to the main spar attachment flanges. The elongation is 1mm, incidently not in the direction where a load is likely to occur. JB-Weld has been used to fill these voids
The 5 or so 4.8mm holes on the RH leading edge skin close to rib 7. The elongation is at most 1mm. This end of the leading edge (will be) fully trapped under the fuel tank skin, heavily constraining any conceivable motion which might lead to fretting. The main structural connection, between the spar and skin 4 is unimpaired. I will decide as to the use of JB-Weld in due course.
One of the upsized 4.8mm holes for the RH wing rib 8 main spar attachment flange: the skin hole is slightly elongated under the doubler: about 0.5mm. No JB-Weld used here.
Some minor elongation of 3.2mm rivet holes along the outer portions of the bottom stringers: about 0.2mm max
Some minor elongation of 3.2mm rivet holes in portions of the rudder, elevator and horizontal stabiliser: about 0.2mm max
All other potential elongations have been avoided by 1) upsizing/recentering and 2) remanufacture of selected parts.
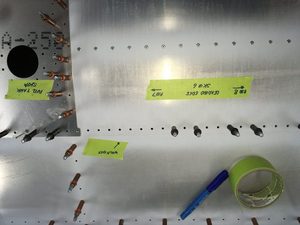
LH wing: The final mismatch which was accepted - not the perfect fuel tank skin fit
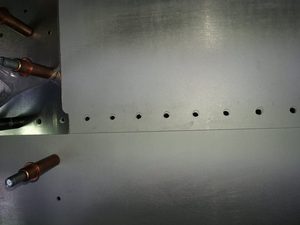
LH wing: Close-up
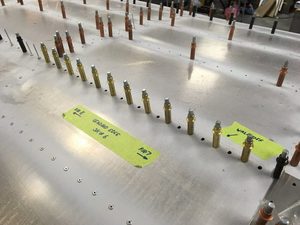
LH wing: After upsizing/recentering
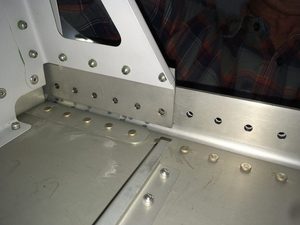
LH wing: Only the bracket holes between ribs 7 and 8 were upsized - these have ample edge clearance (re 2D rule)

LH wing: Skin 4 holes - these all remain perfectly round
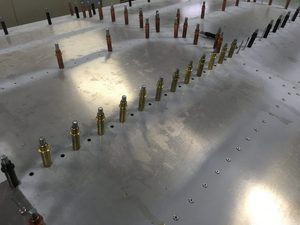
RH wing: Same procedure done
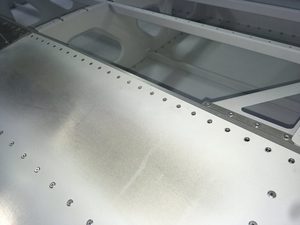
RH wing: after cleanup - note leading edge holes have no residual elongation
This post is from Adam Dickson