Manufacture fibreglass wingtip light bumps
Photo essay
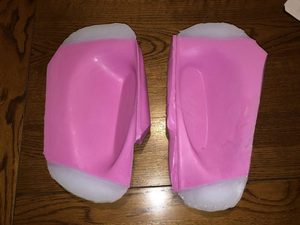
I extended the moulds with silicone rubber to provide a form for flanges
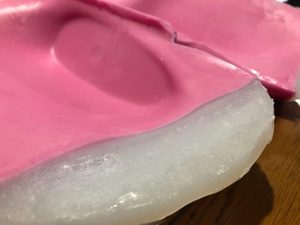
The extensions were also shaped to complete the taper - the mould was a little short. The Silcone rubber was also used to fill defects in the mould.
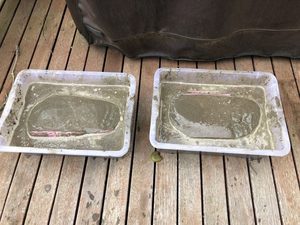
I notices that the moulds - when resting on a flat surface - would deform a little under their own weight. So I immersed them in wet cement+sand so that a support would be created with the moulds in their relaxed state.
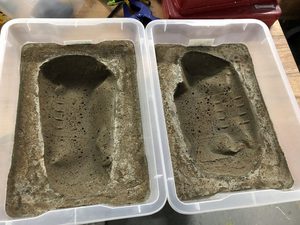
Before the cement was fully cured, I was able to easily extract the moulds
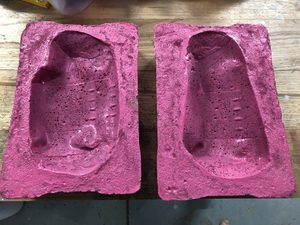
I found that the cement continued to shed a lot of sand, even when more fully cured. This sand tended to get into the mould. So I bound the surface with paint. No, I swear this rattle can paint colour was at hand and that I did not purchase a new can to colour-coordinate!
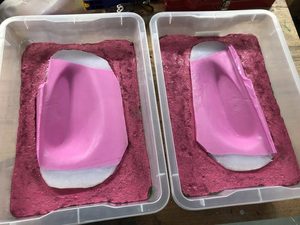
Cleaned and patched moulds ready to use.
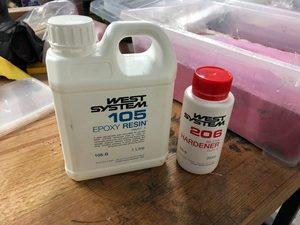
Resin and hardener
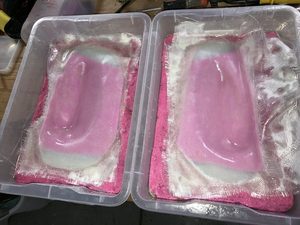
Four layers of fibreglass mat. Sling advised they use three layers in their mouldings, but I chose to aim for more rigidity.
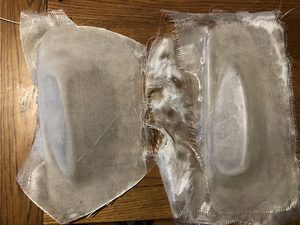
Being silicone, no release agent was required
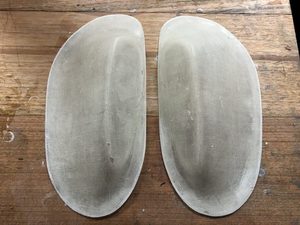
After trimming, exterior view
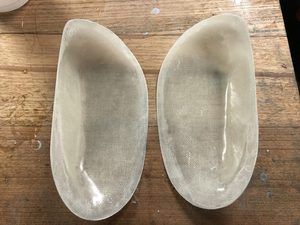
Interior view. I have decided to retain a reasonable sized flange for attachment, and will blend with additional sanding and with gelcoat filler.
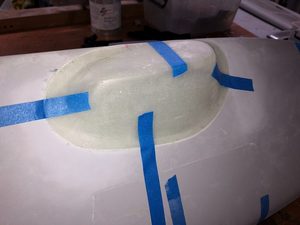
Example fit on one wingtip
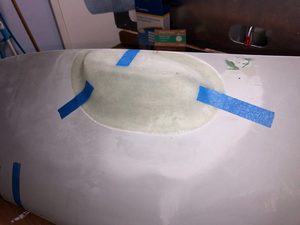
Example fit on other wingtip
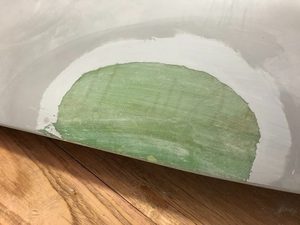
Sanded away gelcoat on one wing
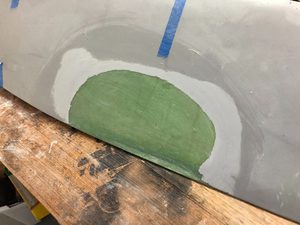
Sanded away gelcoat on one wing, removed a substantial amount of filling. I will cut a large hole in these regions to allow for cable and manipulation of whatever I choose to couple the lamp attachment bolt to (nutplate, rivnut, possibly on a mounting plate.)
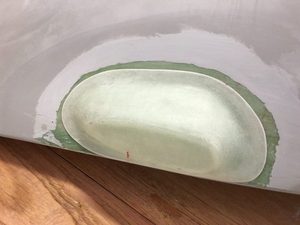
Demo of new wingtip bump in position. Some further smooting of the flanges needed before gluing
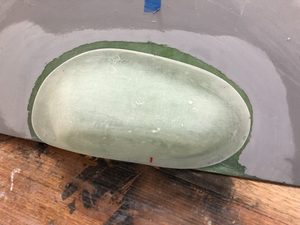
Other wingtip. I may assist the bonding process with embedded countersunk #40 stainless steep rivets
This post is from Adam Dickson