Improving fit of elevator and rudder tips
About a year ago a first pass on determining how the rudder and elevator fibreglass mouldings was done, with some shaping of the trailing tips. These fibreglass items also had a number of bubbles which were (mostly as it turns out) cut out and filled.
The quality fit was revisited. An optimal fit of the elevator and rudder tips was determined, such that any trailing tip fit issues would be solved with flocked epoxy as needed. Holes were made, with care taken to ensure symmetric positioning and orientation of the fibreglass tips. In the event, the fit of the both the elevator and rudder tips needed to be improved, at both the front and particularly the rear tips. The rear tips needed to be built up with flocked epoxy in all cases, as well as lengthened in the case of the elevator in order to reach all the way to the trailing edge of the skin.
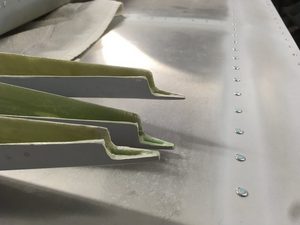
The original tips - which had had some work done on them about a year ago - were slotted
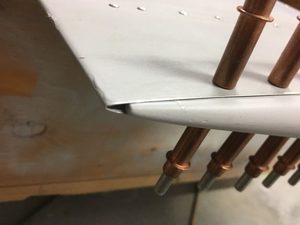
In the case of the elevator they just did not reach all the way
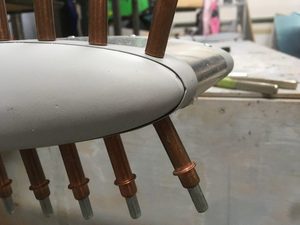
And the front tips did not fit that well either
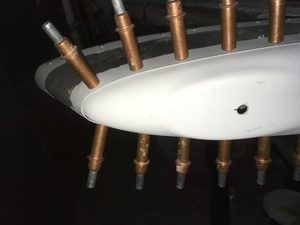
In the case of the rudder the front tip fit quite well
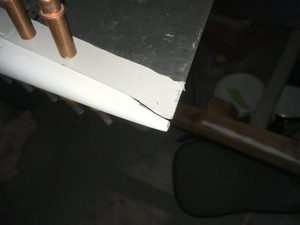
But the trailing tip actually was disconnected from the skin if this fibreglass piece was well situated within the horn skin
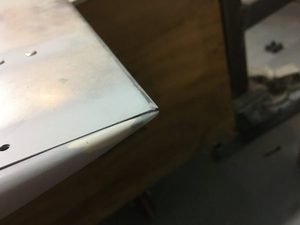
LH elevator, with addtional filler
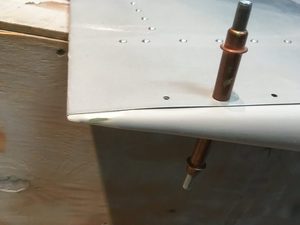
RH elevator, with addtional filler
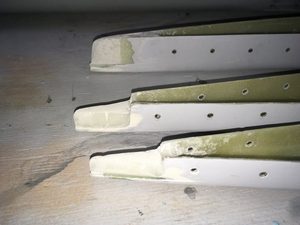
Trailing tips formed with flocked epoxy to ensure a proper keying with the skins, and extension in the case of the elevator to the correct length. The added support also enabled better tapering to avoid bumps in the skin surface
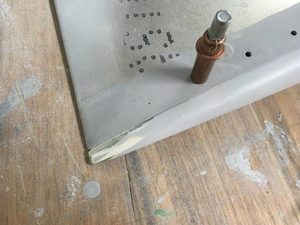
Rudder, with addtional filler
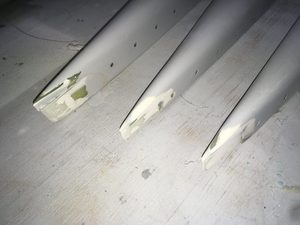
After further fine-shaping
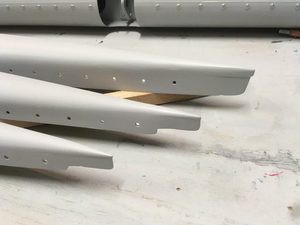
After priming
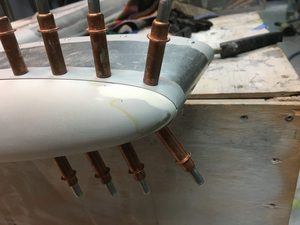
Improved fit of RH elevator front tip
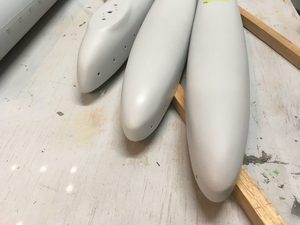
After priming
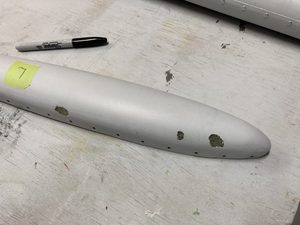
Additional bubbles found in LH elevator tip weave, after cutting out
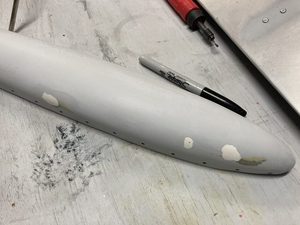
After filling
This post is from Adam Dickson