Fabricate custom floor skin CF-SKN-011
I was shipped a CF-SKN-011-C-A-1 floor skin rather then the C-A-2 indicated in my packing list. The front of the C-A-1 is slightly narrower at the front, about 6.5mm each side. This creates a gap between the side flanges and the side skins which I originally planned to fill with shimming. About 3mm thickness of metal would have been needed at the front of the flange tapering to no thickness at the rear. I planned to make a set of stacked leaves of thinner sheet to create this shim. All of this is hidden from view by the interior skin and otherwise hole alignment was good.
Sling did offer to supply a replacement skin (great service), but I wanted to avoid the inevitable multi-week wait time owing to the size of the container, and possible costs.
I noted the wing step-on skins is made from 0.8mm sheet while this floor skin, including the latest revision are only 0.5mm and I wondered whether it would be a good move to thicken this skin to the 0.8mm level to make it more resistant to concentrated loads. My plan is to stand on this floor as much as possible when embarking or disembarking rather than standing on the nice leather seats! Other builders have considered this question from various points of view.
Since I was ordering sheet for the bottom skin and with shipping being a dominant cost, I also ordered 0.8mm 6061-T6 sheet to fabricate a CF-SKN-011-C-A-2 myself with some dimensional information given by Sling. I would use the original C-A-1 skin as a hole template. I would also drill only those holes as were needed for my toe-brake configuration. The Sling supplied floor skins have many additional holes as they are a universal part, useable also for the non toe-brake configuration.
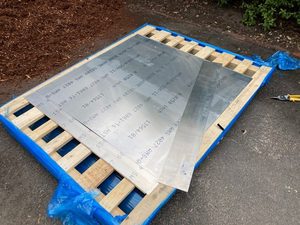
Mill certificates provided
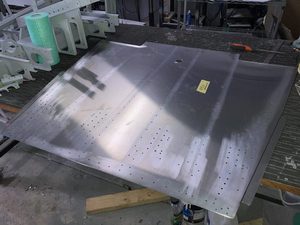
Relevant holes match drilled using the C-A-1 skin as a template
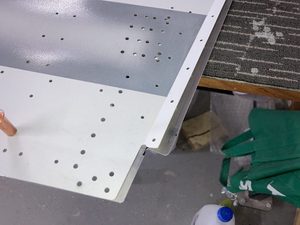
The C-A-2 skin is 6.5mm wider each side at the front of the flange
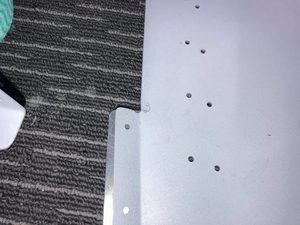
The C-A-2 skin has same width at the rear of the flange (so the flange is slightly rotated, to better fit the side skin shape). I have made the flanges extra-wide here, I'll trim them later
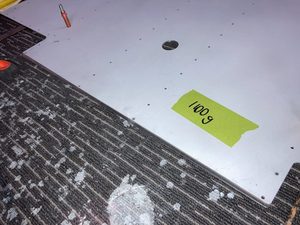
I have extended the custom skin about 4mm rearwards. The clearance is there with the main spar channel. The rivets do not have to be so close to the edge. The primed C-A-1 skin on top, primed weight 1100g.
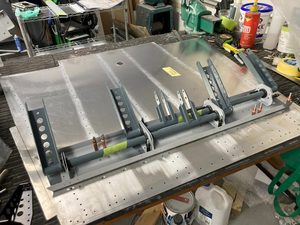
Test fit of the rudder pedal equipment
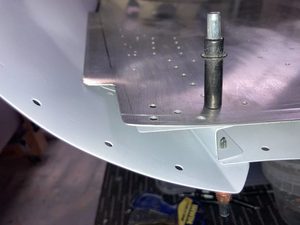
How do I bend the flanges? Here is a first sanity-check test fit, indicating that the dimensional changes are very likely appropriate - RH side
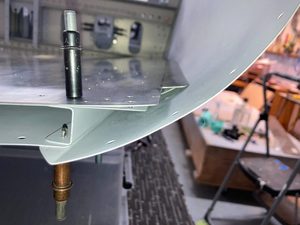
LH side
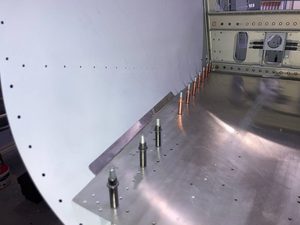
Flange bent using seaming tool. This was done in stages. I found a greated bend was needed at the rear compared to the front, in order to best match the skin. I trimmed about 3mm off the flange so as to better approximate the design. RH side
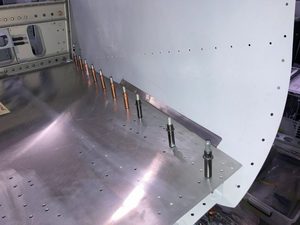
LH side
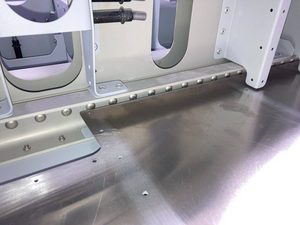
Confirming clearance between the rear edge of the floor skin and the main spar channel
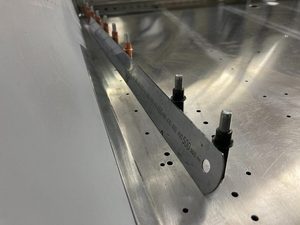
Confirming that skin will lie more or less flat inside the skin. This will improve with a little forcing and after rivetting. RH side
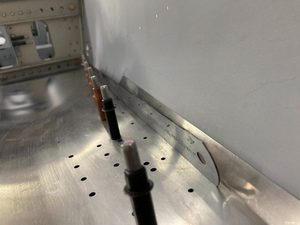
LH side
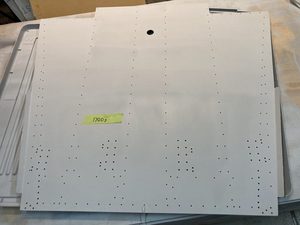
After scrubbing and priming. The primed weight of this skin is 1700g, 600g heavier than the primed C-A-1 skin. This is the expected increase given the thicker material.
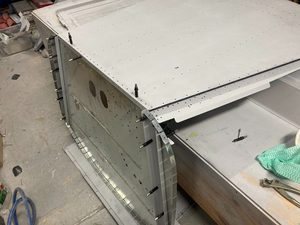
Side effect of thicker floor skin (0.8mm vs 0.5mm) and thicker bottom skin (0.63mm vs 0.5mm) revealed in test cleco of firewall attachment
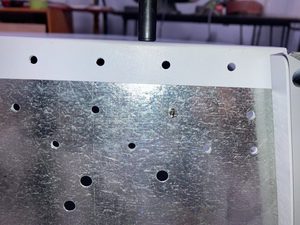
The 0.43mm increased thickess leads to a slight misalignement of these angle holes. This can be handled in a couple of ways.
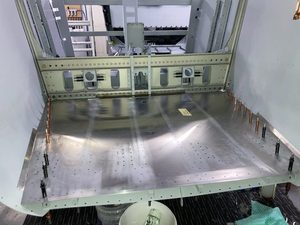
Overall view, before priming
This post is from Adam Dickson