Strategy for installing rivnuts in sheet with inaccessible sound deadener
The front inner side skins are covered by non-inaccessible sound deadening foam. My concern is that setting rivnuts will lead to a suboptimal result, owing to the adhesive layer (yet alone the foam) that will likely be caught between the rivnut and the aluminium. I have found an approach which not only ensures the foam will not get in the way, but also removes the adhesive layer in an annulus around the hole. This result is achieved by access purely through the 15/64" hole from the interior. The procedure is shown on a test strip of 0.4mm 6061-T6 primed and painted as with the inner side skins, with sound deadening foam on one side.
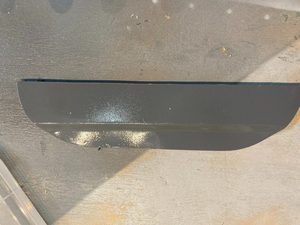
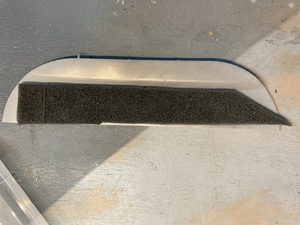

15/64" holes reamed

Foam after holes reamed
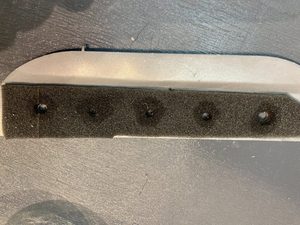
Soaked with turps from other side with a cotton bud
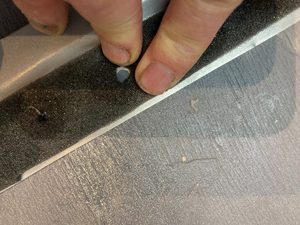
The turps causes the foam to detach, helped along by an edge deburring tool.
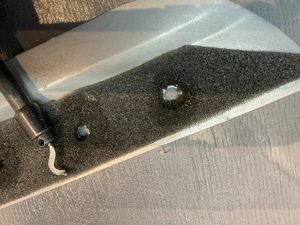
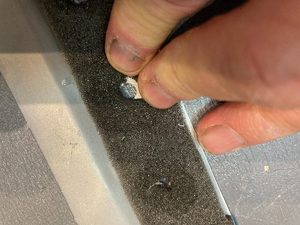
But the adhesive film is still present
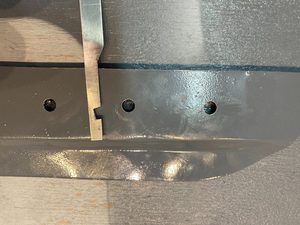
Made a notched too out of 1.2mm 6061-T6 which is inserted from the topcoated side (interior) and twirled around the hold, pulling and angled slightly so as to tear away the adhesive layer.
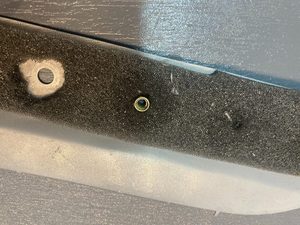
Result of applying the tool accompanied by cleaning with turps with a cotton bud. Note the foam has been pulled away to show the removed adhesive. JB-Weld can then meaningfully be used when setting a rivnut. Here a set rivnut is shown, where the foam has not been pulled away for exposition
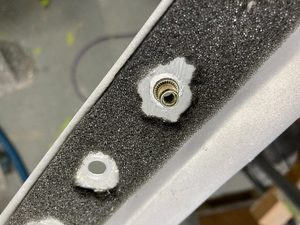
I have pulled the foam away for exposition, here it is clear no foam has been trapped and an optimal connection has been formed (no JB-Weld used in this image)
This post is from Adam Dickson