Tyre tube fitting
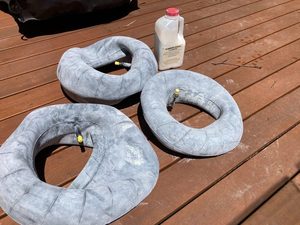
Dusted inner tubes
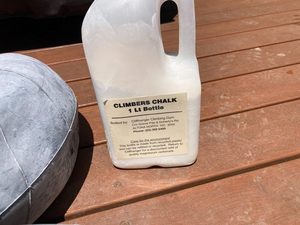
Climber's chalk - very fine powder
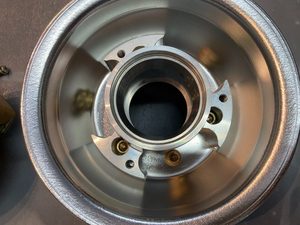
6" main wheel hub after brake caliper removed.
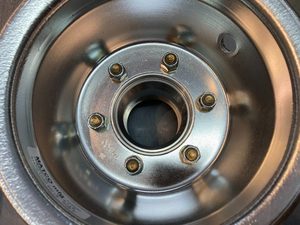
6" hub other side
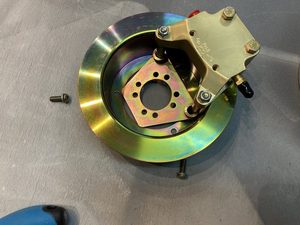
6" hub brake caliper system, torx 30 bolts have Nord-Lock washers
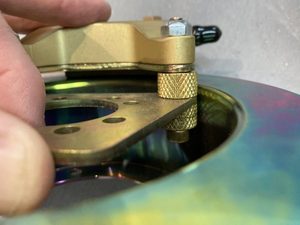
Caliper mounting plate being lifted out - note additional groove in knurled ferrule
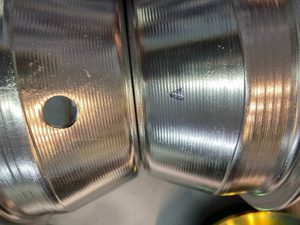
6" hub showing V shaped alignment mark. Also note lack of chamfer around valve tube hole edge
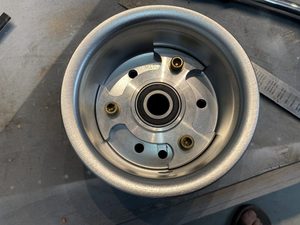
5" nose wheel hub
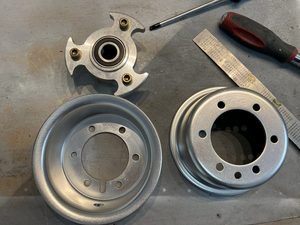
5" hub out disassembly. Note that the milled centre hub holes are also threaded, so it is necessary to ensure these bolts are first torqued into this structure - 120in-lbs - before the nuts are attached.
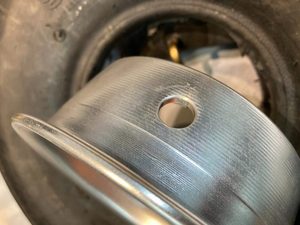
Chamfer applied to 5" nose wheel hub valve tube hole, to prevent chafing against the inner tube
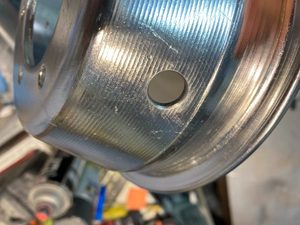
Chamfer applied to 6" main wheel hub valve tube hole. This chamfer ensures the tube is not pinched by not chafed by a relatively sharp corner as supplied. A chamfer also applied to other side, to further reduce chance of chafing.
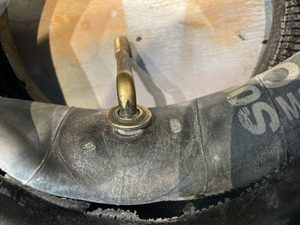
5" hub inner tube came with a stepped washer. There is not much thread to engage with. No way can the washer be located on the outside of the hub.
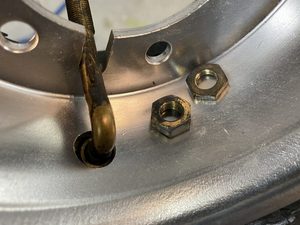
There are two nuts provided. Only the thinner nut is used.
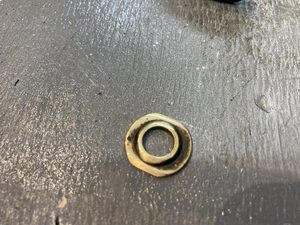
Instead the stepped washer was shaped to sit more closely on the inner surface of the hub. The centre step will ensure the brass tube is centreed in the rather larger hub hole.
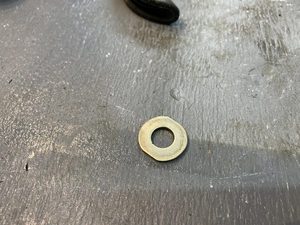
The other, recessed, side of the washer was filed flat.
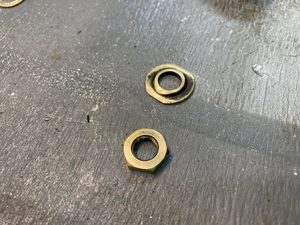
The brass got really thin at the edges of the stepped washer, these edges were filed straight. This also permits a spanner to be used to prevent the washer from spinning as the nut is tightened.
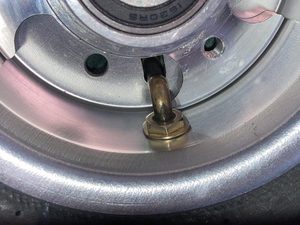
Final result. The nut is not tightened too much so as not to pinch the rubber on the other side too much. This is also why chamfering is important for the nose-wheel in particular. This whole procedure is mostly identical to that used in Pascal Latten's blog.
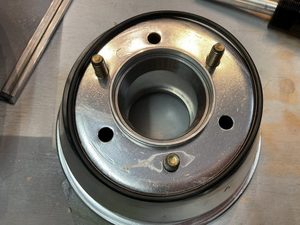
O-ring - coated in slippery water-detergent mix centred over 5" hub
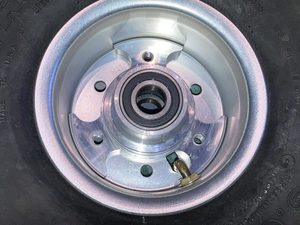
It was easy to close up the 5" hub while checking the O-ring sat in the groove between the two hub halves whitout being pinched. In this and the following images, the machined hub centre is inserted the wrong way around. This is corrected later.
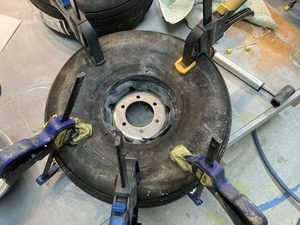
But not so easy with the 6" hubs. Using clamps to maintain visibility of the O rings and ensuring it is not pinched is not the way to do it.
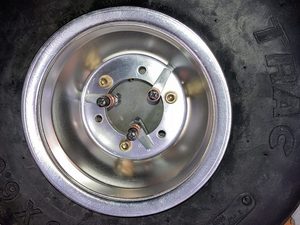
Better to just bring the hubs together by hand, and using cleco clamps to hold the halves together. The halves can then be shifted around relatively as needed, and the O ring if pinched will pop out of the way if needed
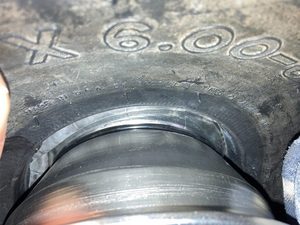
The location - and lack of pinching - of the O ring right around can be easily verified with minimal pushing and shoving of the tyre.
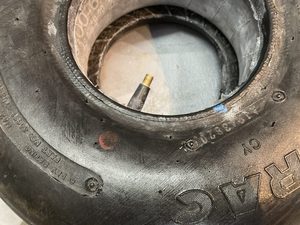
In all cases the red dot is aligned adjacent to the valve. This assists dynamic balancing, as the tyre is slightly lighter in the region, cancelling to some extent the additional mass of the valve
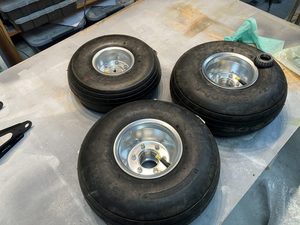
Final result, inflated to 1.8bar, then deflated 50%, then reinflated. All nuts torqued to 120 in-lbs.
This post is from Adam Dickson