Completion of trim tab and fixing of tolerance issues
Simple clecoing of the trim tab parts led to a situation where there was 2.5mm clearance between the curve of the skin and the hinge knucle at one end, dropping to zero (contact) at the other end. A systematic approach was taken to chase the errors out of the parts:
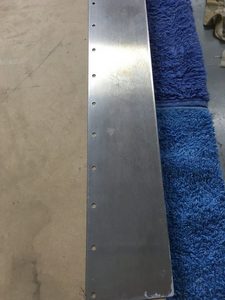
Distance between holes and edge on flat part of skin was constant along the edge.
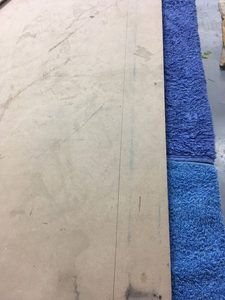
A guard was made out of 3mm MDF to separate the jaws of the skin
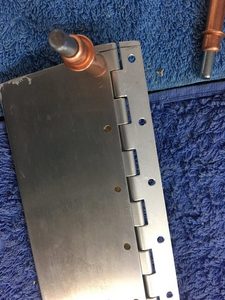
This guard was inserted along with the hinge and the edges of the notches of the hinge lined up with the edge of the skin flat. Mismatch between the skin and hinge holes could then be drilled out, the mdf protecting the lower jaw of the skin
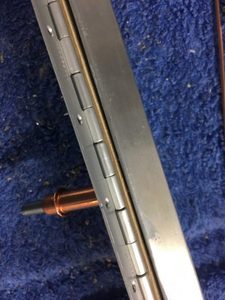
Side view
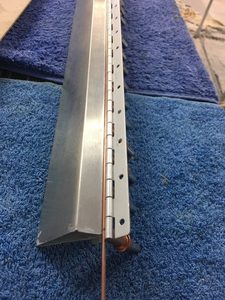
The guard was removed and a 2.4mm welding rod was then inserted which enforced a separation between the hinge knuckle and the curved extremity of the skin. With the help of clecos, clamping etc the upper skin is bought back into alignment with the altered hinge holes revealing those parts of the lower jaw skin which would have to be drilled out. This was done and the result deburred with Vlies 320 grit. The trim tab was then clecoed together using 1.6mm rod inserted into the hinge gaps to recreate the required flexing of the lower jaw (particularly in the centre). All three holes would be bought into alignment. These were topped off with a #30 drill and the outer skin deburred.
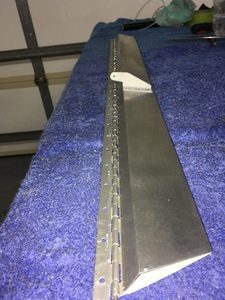
The result after riveting, showing hinge knuckle clearance
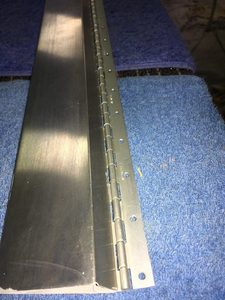
Other end - very happy with result. Hinge rotates freely
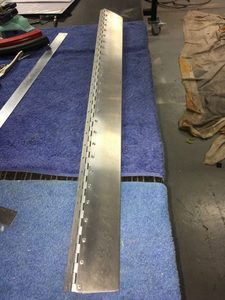
Top View
This post is from Adam Dickson