Working On Various Parts
Worked on various random elevator parts. Back riveted the nutplates to the trim tab servo reinforcement plate. Van's gives the option of either dimpling the nutplates and attaching them with AN426-3 rivets or using NAS1097AD-3 rivets with a small countersink in the plate and thus no need to dimple the nutplate. Since NAS1097 rivets aren't supplied I used the former method, dimpling the nutplates and back riveted them uneventfully. And they came out fine. I looked on the VAF Forum and there were many opinions on the pros and cons of either method. I can certainly see the advantages of using the NAS method. Since there are many more nutplates in my future, I purchased some NAS1097AD3-3.5 rivets from Wicks to have on hand for the next time. I also completed the trim tab pushrod. This part seemed overly complicated as it consisted of 3 separate metal strips that must be cut out, finished, countersunk both sides and double flush riveted. Took hours. I mean, it's only 5 inches long. I broke my bandsaw blade in the process so ordered a new one of those. Seems like a simple one piece steel rod with clevised ends would work just as well and weigh about the same. I'm sure Van's has their reasons. While fabricating it I had an epiphany regarding my 100 deg countersink hex shank. I have it mounted in a cheap cordless screwdriver and have used it strictly for deburring holes. In spite of the name it never occurred to me to use it for making countersinks. I've always used my microstop countersink tool for that. For some reason it dawned on me that I could use the hex shank in the screwdriver for cutting holes. It worked great for the 8 holes I had to cut in the pushrod. Quick and clean. Kind of a Duh! moment. I'm sure they're be more in the future.
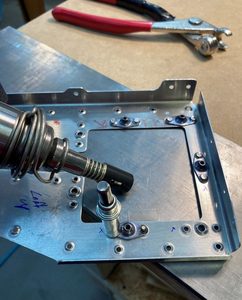
Using my back rivet plate and rivet set for the nutplates,
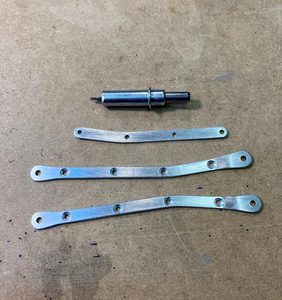
Had to cut and clean up all the pieces. I clecoed them together while sanding the edges to keep the edges true.
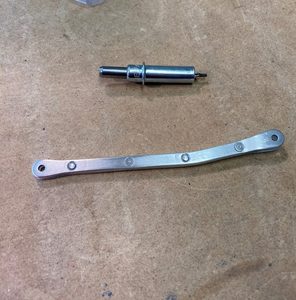
I alternated the double flush rivets.
This post is from Scott's RV-14 Build