Day 38
Nose Gear & Cabin Air
Today we were able to finish assembling our nose gear. We removed material from the inside of the bushings until they fit around the shaft. This proved to be a bit of work. The composite material that they are made of does not sand easily. We ended up taking 80 grit sandpaper wrapped around a drill bit and working the inside surfaces. Once they were very close to fitting, we then used 220 grit sandpaper to finish, which brought the back to being smooth. Once they were fitting properly the two locking bolts slid into place perfectly. We were careful not to remove too much material. It was important that the bearings still be snug, but that the nose gear be able to turn easily without the bearings moving.
Once we had the retaining strips bolted in place and snugged up, we continued on with the rest of the assembly. This included riveting on the lower cowling angle bracket, bolting on the nose wheel fork and Tow Bar brackets (which also required tow M5 rivet nuts), and installing the control rod ends. With all these completed all that is left for the nose gear assembly is to install to wheel hub and tire once our back ordered O-rings arrive.
We also sealed up our heater air ducts and NACA ducts today. We had done some preparation for this by scuffing the channels along the inside of the fuselage walls where the warm air from the heater will travel for the rear passengers. We went back over everything to make sure it was all good to go and cleaned all the surfaces. We also trimmed about a 1/4 of an inch off of the upper lip of the heat channel so that it would fit in properly against the fuselage angle riveted to the side of the fuselage.
Once everything was prepped and cleaned, we applied small beads of SikaFlex along the channels and smoothed everything out, filling in any small gaps.
We then fitted the NACA ducts to the side walls. Once the holes were match drilled, we then counter sunk the holes on the composite material. We also ended up adding one more hole on the aft portions of the ducts because the one on the left didn't fit as well and needed an extra rivet. We did the same to the right to make them match. We 3D printed some reducers and caps as well. From the factory they have a blend air system for the heat and fresh air, which in theory is a good idea, but in execution doesn't work very well. Most builders will bypass it and run outside air directly to the dash and use the feet ducts for heating the front. This is why we capped of the back of the "T" pieces. Then the reducer is to help create more air pressure and fit the duct tubing for the dash panel.
We put some SikaFlex around all these parts and smoothed them all out filling in any gaps. We then put a small amount around the NACA ducts and riveted them onto the fuselage side walls. Once all the SikaFlex was smoothed out we went around and cleaned up all the outside surfaces and made it all look nice and clean!
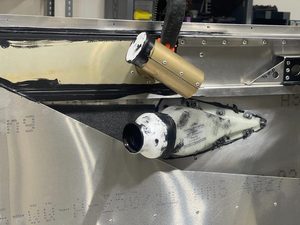
Close up detail of the NACA duct and heat channel with the fitted and sealed 3D printed parts.
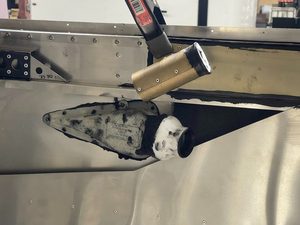
Close up detail of the NACA duct and heat channel with the fitted and sealed 3D printed parts.
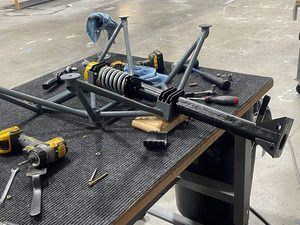
Assembling the nose gear on the motor mount.
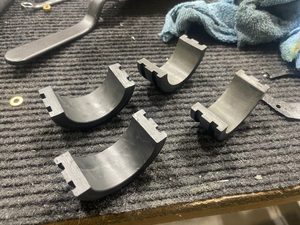
Sanded nose gear bushings.
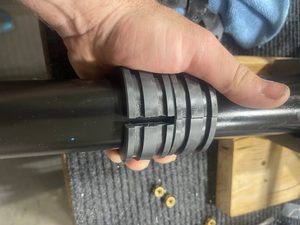
This was the difference between the fitted bushings (top) and the unfinished bushings (bottom)
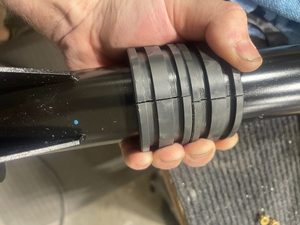
This is what the bushings looked like when we had them fitting the nose gear shaft.
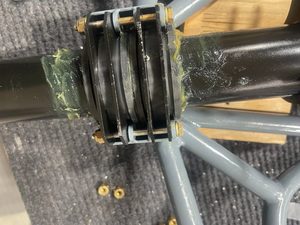
Greased up and fitted lower nose gear bushings with the bolts in place. The nose gear now turns smoothly.
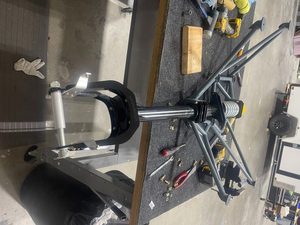
Putting the Wheel Fork together.
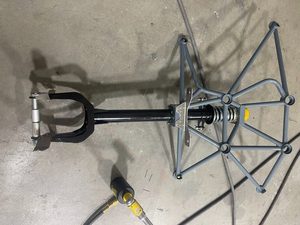
Completed nose gear assembly.
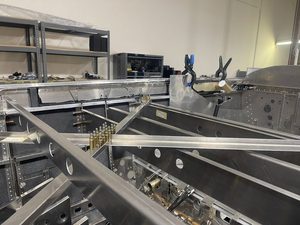
Rear view of sealed heat channels.
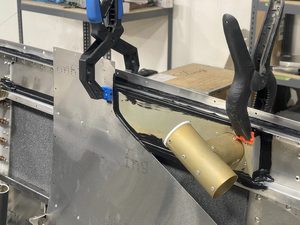
Using clamps to hold pieces together until the SikaFlex cures out.
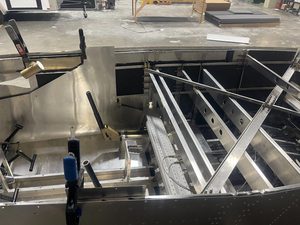
Sealed up rear passenger heat duct channels.
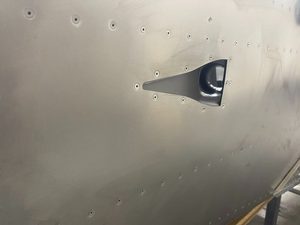
Inlet for the NACA ducts after riveting them on and cleaning up the SikaFlex.
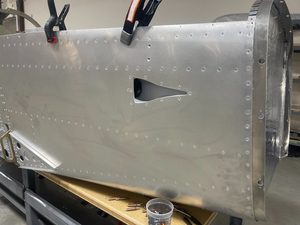
Inlet for the NACA ducts after riveting them on and cleaning up the SikaFlex.
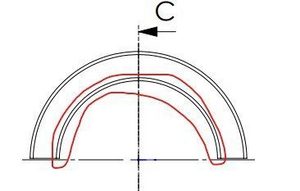
Where we removed material from the inside of the nose gear bushings