Wing fuel tanks part 3 - ribs 1 and 5 hardware installation
Photo essay as follows. One point worth mentioning is that the class B2 selalant was used well past the 2 hour minimum pot life, more like 4 hours and some needed rework at over 5 hours. Apart from being stiffer and with less flow, the ability to apply this sealant usefully was not appreciably impeded, particularly for the applications here. There was some cross-linking but no loss of stickiness throughout, and would relax to a shiny state. The final buildups around the AN fittings look a bit dull in places as much later I was cleaning threads of residual sealant and the now-tacky material picked up finger-prints etc and would lose gloss to the solvent.
Note that 20mm diameter washers were made from 1mm 6061-T6 to backstop the machining holes, in turn riveted with 4.8mm sealed rivets.
Note that buildup of sealant around and over the AN6 fittings and nuts on both the interior and exterior surfaces while not so pretty is an attempt to maximise the strength of the connections, against torque loading (note there is no place for a spanner on these fittings) and consequent spin out. Of course the internal bracing will do most of the work. I have no experience with this sealant - I have no idea how useful it may be in this role or will just be ugly for no reason.
The fuel inlet grilles were verified free of sealant and other debris.
The copper fuel inlet flares were torqued dry (no lubricant to keep it away from this environment), to 70 in-lbs, first once (to form the flare a little) then twice. In fact these connections are not so critical, and absolute integrity is not paramount (they are right next to the inlet grilles).
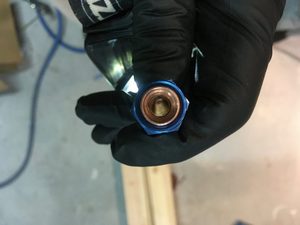
Checking fuel inlet tubes are free of debris
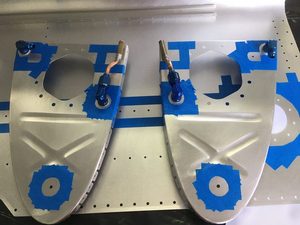
rib 1 interior
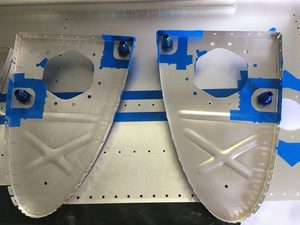
rib 1 exterior
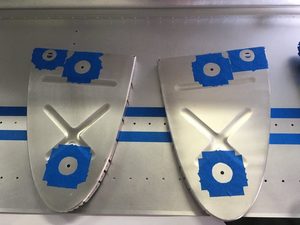
rib 5 interior
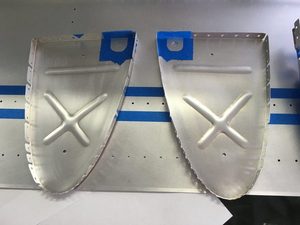
rib 5 exterior
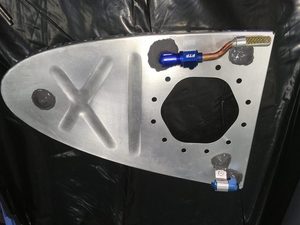
rib 1 complete interior
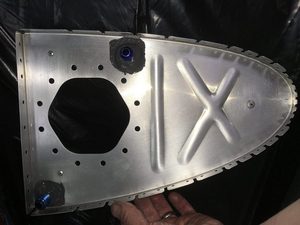
rib 1 complete exterior
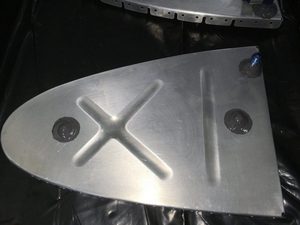
rib 5 complete interior
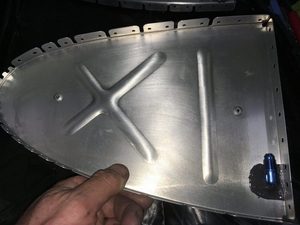
rib 5 complete exterior
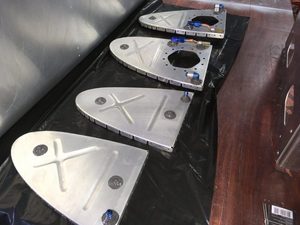
Overall result
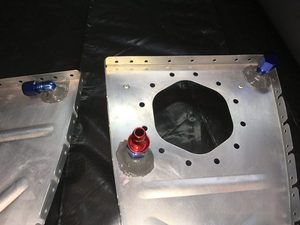
AN4 and AN6 fittings purchased for later fuel tank pressure testing. These fittings also verify sufficient thread available.
This post is from Adam Dickson