Improved bracing for the fuel return fitting
AC43.13-1B calls for AN6 flared fitting to be torqued to 110-130 in-lbs. I found after assembling the ribs with the fittings previously that the fuel return bracing could not withstand this torque under compression - as would happen in the left wing fuel tank - and was close to collapse. Under tension - for the right wing fuel tank - it just survived but would distort. The problem is the small moment arm - at about 1". The fuel inlet bracing - with a moment arm of close to 4" - was fine.
I queried the Sling builder forum and was assured that these fittings would not be so torqued, instead just closed to the point of "nipping". The build manual does call for 577, and maybe - although I am not sure - the fuel hoses have a 1-part construction with a closed cap structure. This is not true of the AN6 flared coupling which I do have which have a 2 part construction which critically depends on the flare to achieve a seal.
So I decided to remove all doubt and upgrade the fuel return bracing so it could withstand 110-130 in-lbs. This was achieved with the same 45 degree bracing angle, but now a wider structure made from heavier 1mm 6061-T6. Two rivets now brace the midpoint, and the attachment to the rib is also now with two 3.3mm sealed end rivets. This creates a large margin against shear failure of these rivets under load and also stabilise the structure considerably. These rivets shear at 1050 N = 236 lbf each, a total capacity of 472lbf. The total force on the mount under full torque (arm is about 0.8") is about 162 lbf, for a large margin.
The use of a single sealed rivet is retained for the fuel inlet bracing, which is unchanged. With a 4" moment arm, under full torque the shear force on this rivet is just 32 lbf.
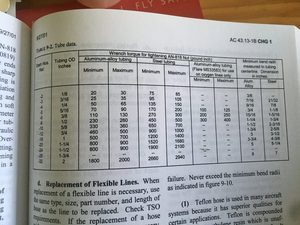
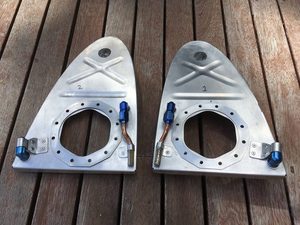
test run
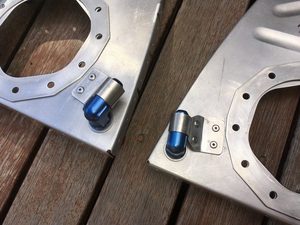
This post is from Adam Dickson