Correction of wingtips part 1 - Attachment of custom fibregss wingtip nav light bumps
Photo essay. Much fiddling was done with the bumps so as to make their position and orientations as similar as possible between the two wings. Some compromise had to be accepted here, and some particularly persistent differences had to be absorbed by increasing the degree to which the lamp could be rotated (by increasing the size of the cable access hole to 5/16"). I aimed for as much similarity as possible in 1) how far the bump tuck out at the front; 2) how far inset at the rear; 3) who far below the top edge of the wingtip is the mounting hole; 4) the degree of vertical-ness of the lamp mounting plane. I had to accept that the bump outlines had a degree of rotation that was not entirely complementary. This last issue can however be obscured by rotating the lamp itself, as stated earlier, a move made possible by the fact that the bump area is considerably wider than the lamp itself. Finally, I noted that the orientation of the mounting plane is not exactly lined up with the axis of the aircraft. In fact the lights will be pointed slightly rearwards. This is however not an issue, given the angular width of the beam. I think, but am not sure, that the rev 1 wingtips have this same property - the moulds do suggest so.
Enough cotton flock was added to make the epoxy into a white paste, but not so much as would be needed for fully self-supporting structures.
The TH wingtip had a big groove near the outermost edge (originally filled in the supplied wingtip). The epoxy/flock combination worked well to fill this.
When cured I will remove the rivets, and blend and fill the transition using a combination of sanding and gelcoat filler.
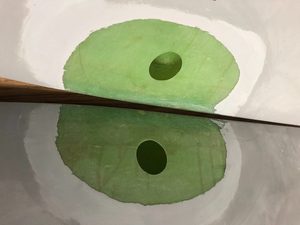
Gelcoat removed and access hole cut in each wingtip
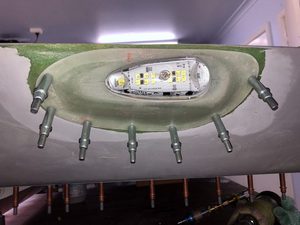
RH wingtip bump position finalised, with 2.4mm reference holes drilled - clecoed in place
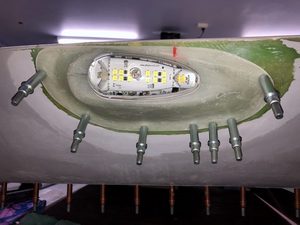
LH wingtip bump position finalised
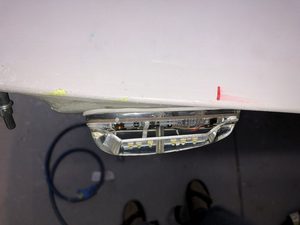
LH bump, top view
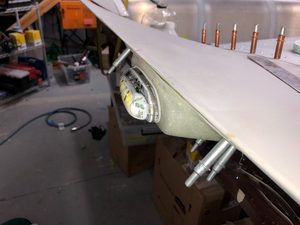
RH bump, front view
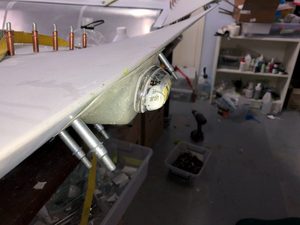
LH bump, front view
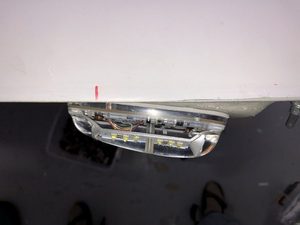
RH bump, top view
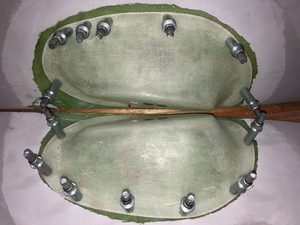
Similarity of bump shapes and position, top view
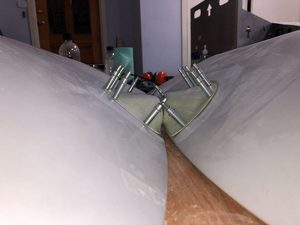
Similarity of bump shapes and position, front view
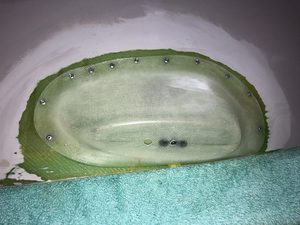
LH wingtip epoxied and held in position with 2.4mm Al/steel rivets. The epoxy was blended with cotton flock to ensure it held shape and did not flow. The rivets will be removed once cured and the holes filled with epoxy/flock
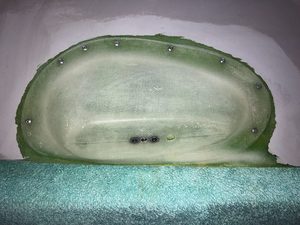
RH wingtip epoxied and held in position with rivets
This post is from Adam Dickson