Positioning and drilling of wingtips
The wingtips are very close in shape to each other, but some small differences led to some compromises being made in the positioning. After ensuring the bases of the wingtips were at precisely the same level, the wingtips were positioned such that the raised trailing tips were also at the same level, all done using a laser level. Nominally, the wingtip body top surface should also be flat along a line extending the main spar. I found that this could be achieved with the RH wingtip, but a slight raise of a couple of mm had to be accepted with the LH wingtip. In fact the LH wingtip had a slight rise and fall.
In order to get to this point, it also had to be ensured the wingtips were inserted optimally into wing-end, ensuring maximum distance between the fibreglass edge and rivet holes that are to be drilled in the fibreglass. I found it necessary to trim up to 2mm of fibreglass in places to ensure the as much as possible, also ensuring the fibreglass butts against the flanges of the outmost rib 11 as much as possible. Even after doing this there was enough variation in the way the fibreglass was cut at manufacture that in some places the fibreglass edge would be unavoidably too close to the rivet holes that would be drilled, as little as 6mm rather than the preferred 9-10mm. This fibreglass would have to be built up later.
Additionally, despite using straps to pull the wingtips forward as much as possible, gaps (as noted previously) exist between the leading edge skin and the wingtip, as well as considerable shape mismatch between the tails of the wingtip and the wingtip skins 8. This will also be dealt with later.
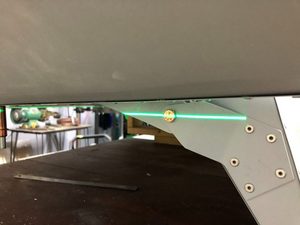
LH aileron bolt
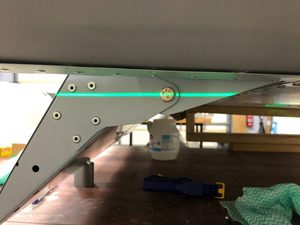
RH aileron bolt - along same line ensuring the wings are at the same level
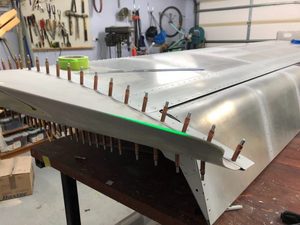
LH wingtip
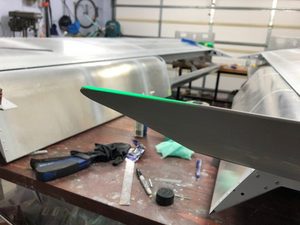
RH wingtip
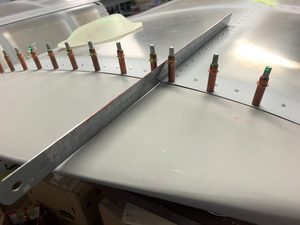
RH wingtip along extended main spar
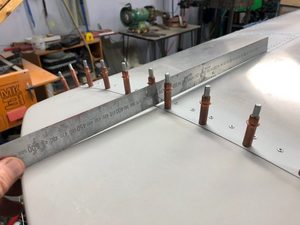
LH wingtip along extended main spar - slight raise evident
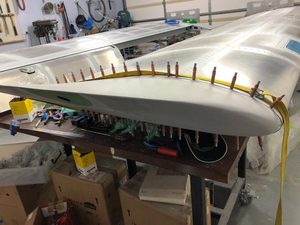
RH wingtip clecoed in place, after drilling
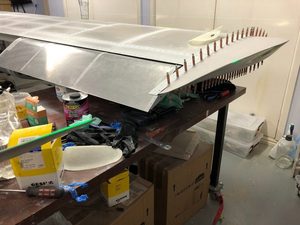
LH wingtip clecoed in place, after drilling
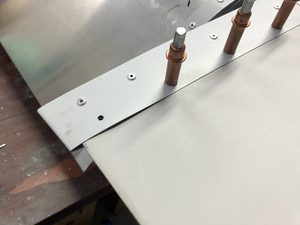
RH tail mismatch, top
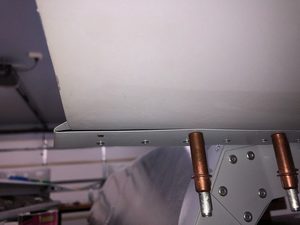
RH tail mismatch, bottom
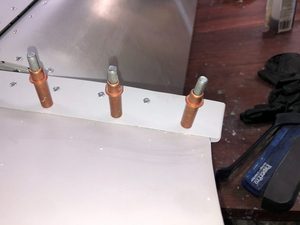
LH tail mismatch, top
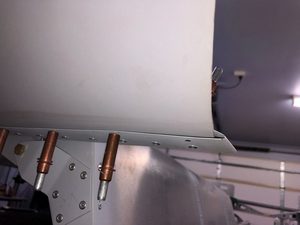
LH tail mismatch, bottom
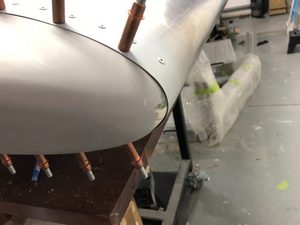
RH leading edge mismatch - minimal
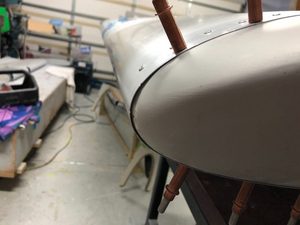
LH leading edge mismatch - slightly worse
This post is from Adam Dickson