Starboard and Port Wing Construction
Starboard and Port wing construction. The Spars are of composite materials completed at the factory. Due to pitting found on the spars themselves, I elected to sand the spars and anywhere a pit, gap, or crack was found, I elected to use structural fiberglass flox to fill them in with. A final sanding was performed in preparation for the installation of the factory supplied ribs. The next item to be completed is the attachment of the wing skins. The ribs and the wing skins were bonded using a Micro/Epoxy slurry.
There were some problems I found upon inspection of the spars and instructions. The first issue I discovered was that the Spars were marked incorrectly at the factory. The left spar was marked on the right spar and visa versa. The next problem was the location of the first rib that was pre-marked at the factory. I am glad I did a dry fit with the first rib in place on the spar. When I placed the spar into the fuselage, the rib location on the spar was completely off and therefore had to be remarked the right way.
It pays to check and then recheck. A builder should be able to trust what the factory tells them but In my case this was not so. I learned a valuable lesson and have triple checked every instruction printed within the manual.
Next came the internal components such as the bell cranks and associated hardware. Control linkages, rods, flap and aileron hinges, tie down fittings, and access panels al had to be completed.
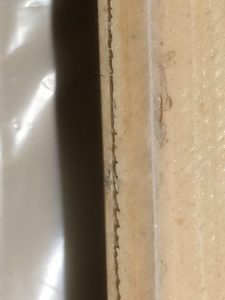
A gap in the upper spar cap is found. Probably a result of when the spar was separated from the mold at the factory.
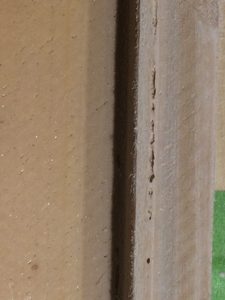
More gaps.
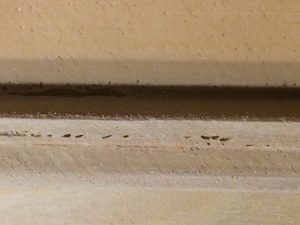
Slight Pitting in the upper spar cap.
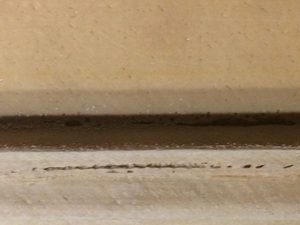
Another gap line found.
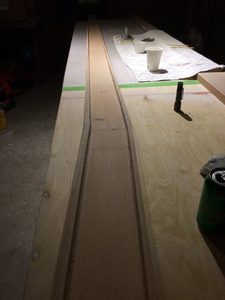
My Starboard spar being prepared for gap and pitting fill.
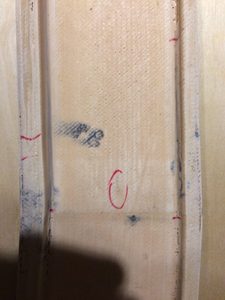
Pits and gaps were marked with a red sharpie.
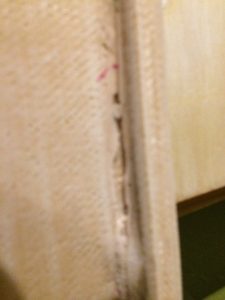
This picture shows some extensive pitting.
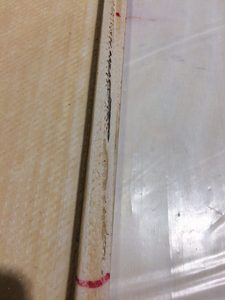
Another major concern found in the upper spar cap.
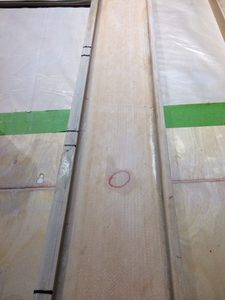
An indention that has already been filled with flox.
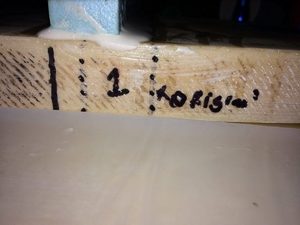
Picture shows the original location of rib number 1 as marked with the dotted lines. The sold line to the left is the inboard line corrected for rib number 1 location.
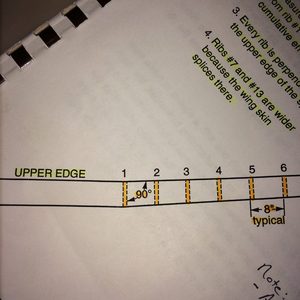
The manual shows the correct layout of the rib locations. there is 7 inch spacing between each rib. There are a total of 17 ribs.
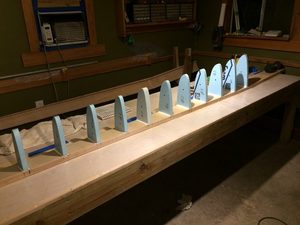
Picture showing Ribs 1 through 11 after bonding.

Ribs 11 through 17 after bonding.
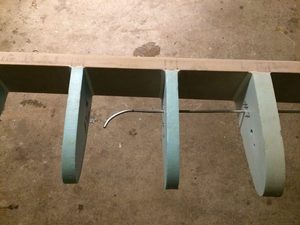
My aluminum Pitot tube that goes from rib number 1 through rib number 8.This is a dry fit of the Pitot tube. Pitot tube will exit the bottom of the wing in a traditional configuration. The plans called for the tube to exit the leading edge. I didn't like the way that looked so I decided to do it through the bottom instead.
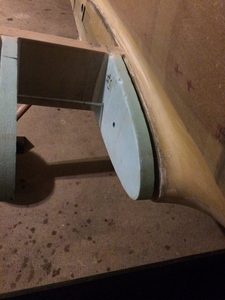
As you can see, rib number 1 has a good and tight fit against the fuselage. The Pitot tube is visible between ribs 1 and 2.
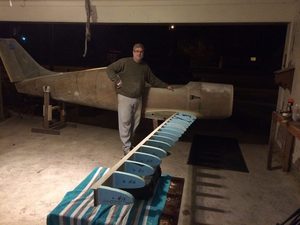
A complete view of the dry fitting of the leading edge ribs on Starboard wing.
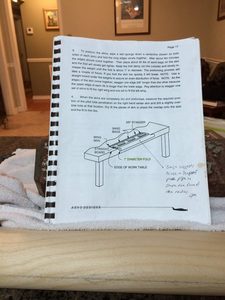
Manual instructions for wing skin forming.
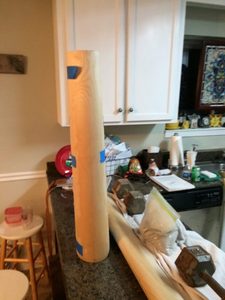
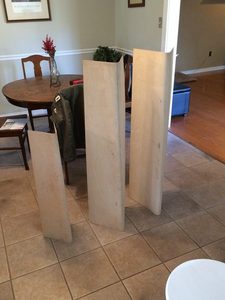
All three leading edge wing skins preformed and ready for installation.
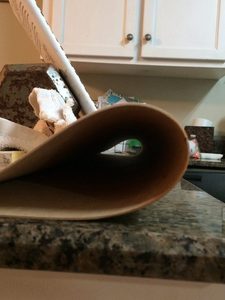
Leading edge wing skin being preformed.
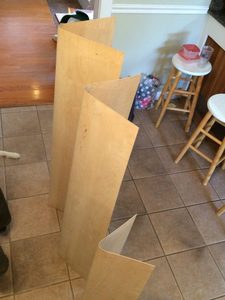
A closer look at the leading edge skins preformed.
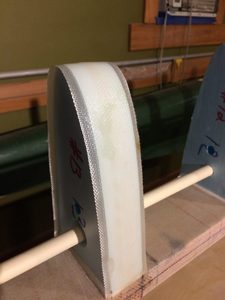
Each location where the wing skin is supposed to butt join the adjacent wing skin the rib is covered with 2 inch glass tape.
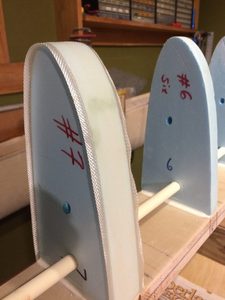
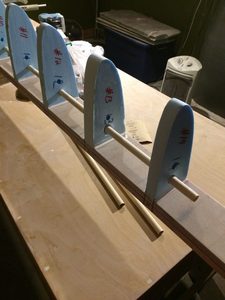
After careful thought and a fair amount of research, I decided to use PVC piping as conduit for housing and routing of the Navigation lighting that will be installed later. I was sure to drill drainage holes every foot to wick away any moisture that might build up within. I secured the conduit in each rib with a micro slurry. Turned out to be just what I needed. I also made certain to smooth any sharp surfaces on the conduit.
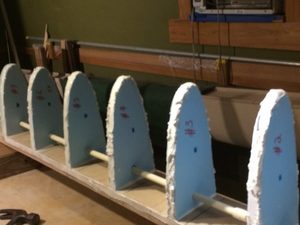
Getting the nose ribs covered with micro for skin bonding.
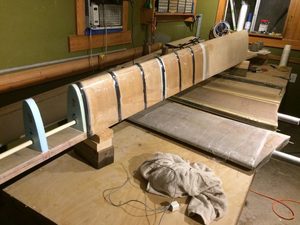
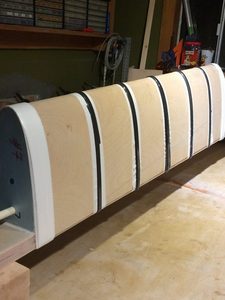
Used Electrical tape to apply pressure to the skins for drying. Careful application of force is a must for uniformity!
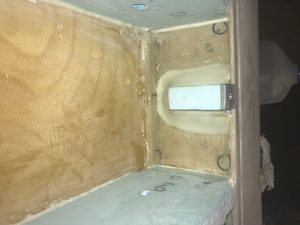
Tie Down Fitting Mounted. Metal fitting has been drilled and tapped in order to accept the stainless steel loop bot. I also covered the blue area which is some rib material that was added to keep the critters from catching any free rides down the road. I simply coated the blue with a slurry of milled fiberglass
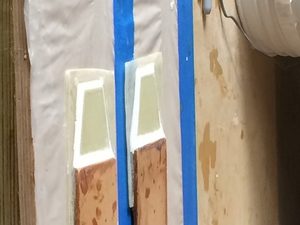
Attachment Plates for the Rear Spars.
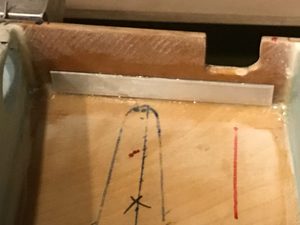
Undressed cutout of flap control linkage.
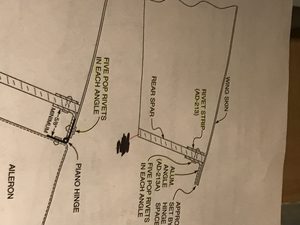
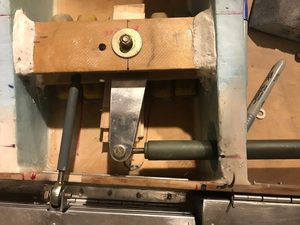
The alignment passes inspection. Now time to add strength to the junction where the ribs meet the wooden plates on the aileron bell crank.
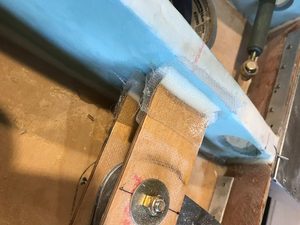
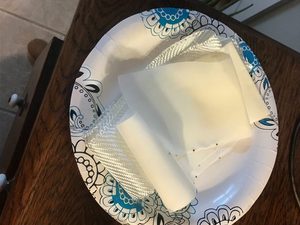
Fiberglass cloth and tape along with some peel ply for wing construction.
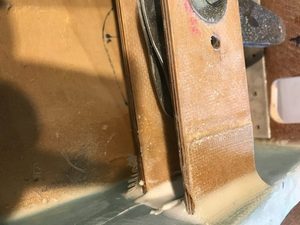
Pretty crude by design. I am modifying the ribs and glass content to strengthen.
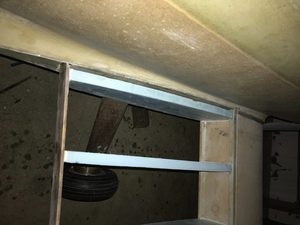
Dry fitting the Starboard wing with rear ribs in place. Looks a good fit. Now time to get it skinned.
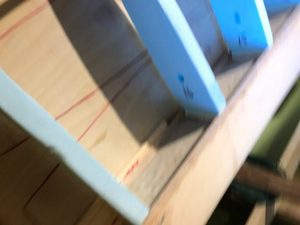
Wlak pad interior before secured in place.
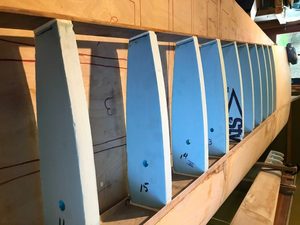
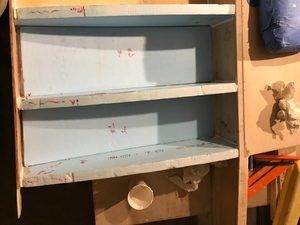
The plans call for the application of a section of rib material high density foam laid between ribs 1 and 2, 2 and 3, with wing skin on top of that. All micro slurred into place. The final step was to apply fiber glass cloth over the wing step bottom.
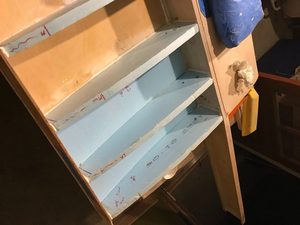
Wing step construction. Adding the step pad per the manual's instructions.
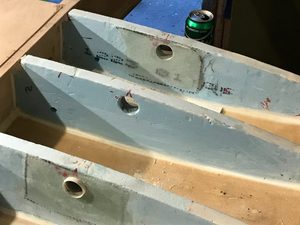
Undressed Flap actuation area.
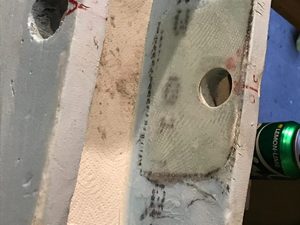
The plans call for making the reinforcement pad for the flap actuating rod that you see in this photo. I decided to expand on this as it yet again seems crude,
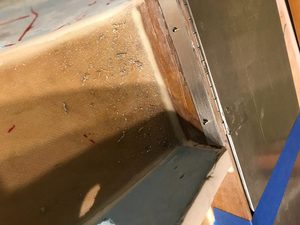
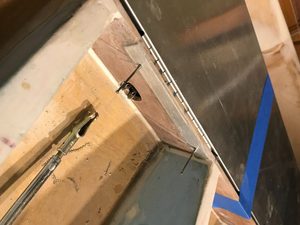
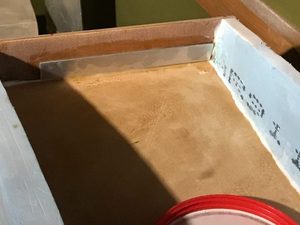
Aluminum strip installed for a solid surface for riveting the control hinges to. I adhered the aluminum to the rear spar with Aero-Poxy structural epoxy. I should add that the process of adhering aluminum to other materials like wood is very strict in preparation and procedure. First the aluminum is scuff the side to be epoxied really well to give the epoxy a better mechanical bite. After a complete scuffing, I then wash the aluminum using Comet along with a scotch brite pad and carefully and completely rinsed with water careful not to touch the aluminum with my fingers as fingerprints can greatly reduce the bond strength. .
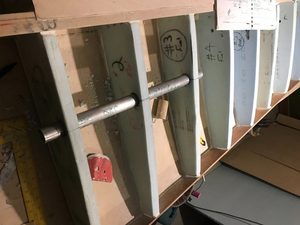
Fitment of the flap actuating rod and its bearings.
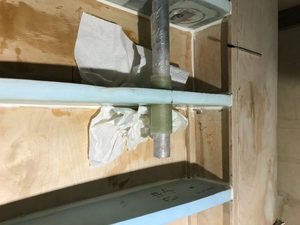
Another view of the fiberglass bearing construction method.
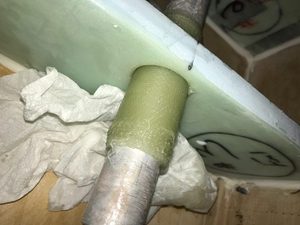
Making bearings using four inch glass tape.. I covered the flap actuating rod with several coats of Mother's car wax and then wrapped the tube in cellophane just for good measure. One thing you don't want to happen is to have that damned rod stuck in place because you will never get it free.
This post is from Clyde Oyler's Pulsar I