Flying the Bearhawk - Cruise
Cruise speed
The cruise speed is largely dependent on engine size, tire size, and whether operating lean of peak or rich of peak. These all have an effect on fuel economy. My aircraft has an IO540 with PMAG ignitions, with 26" Goodyear tires. How the aircraft has been rigged also affects its cruise speed.
Whenever possible I operate the engine Lean of Peak. This reduces power and speed, but vastly increases efficiency.
A typical cruise setting would be 2200rpm and 23" MP with a fuel burn of 38 lph LOP. At lower altitudes this gives about 115 KTAS, and about 130 KTAS at higher altitudes.
The Bearhawk with an IO540 can easily be flown in normal cruise between 100 kts and 130 kts TAS. Even at low altitudes the speed can be increased to 130 kts by flying ROP at 55 lph.
Comfort
The Bearhawk has a low wing loading. Any turbulence is felt more than in aircraft with higher wing loadings, particularly at the higher end of its speed range. If flying through turbulence, reducing speed often improves comfort.
Slow flight configuration
The aircraft can be slowed to 70 kts and with F2 selected it flies well with good visibility for a low weather configuration.
Fuel Management
My aircraft and many Bearhawks have a fuel system with a L-BOTH-R-OFF selector. BOTH is the preferred position. This allows fuel from one tank to flood the ports even when the opposite side tank becomes unported. However even when operating in the BOTH position it is important to maintain balanced flight for a number of reasons. If the aircraft is flown even slightly out of balance, it will burn more fuel from the side that provides the higher head pressure. This can result in a flow between tanks via the fuel selector.
A Bearhawk safety bulletin states:
The Bearhawk Fuel System as shown in the Bearhawk Book is designed for use without a fuel pump.
If a fuel pump is used, extra care in flying is required so that neither main tanks become unported, as a fuel pump would rather suck air than fuel.
If one tank is very low and the other is not very low, set the fuel selector on the fullest tank and fly the plan as not to unport that tank.
Rudder
The Bearhawk vertical fin is slightly offset to compensate for the prop-factor from a clockwise rotating propeller (when viewed from behind). It creates a right turning tendency to compensate for the left turning tendency created by the propeller. In addition most aircraft have the rudder trimmed (permanently) to provide balanced flight at cruise speed.
Therefore if flying at a speed slower than normal cruise speed it requires slight right rudder input, and at a speed above trimmed cruise speed it requires slight left rudder input. The Bearhawk rudder tends to be super sensitive, and maintaining balanced flight takes some practice initially, so it was common for me to have an uneven fuel burn during the early flights. Once I got better at maintaining balanced flight the fuel burns were much more even from both tanks.
The easiest way to check this is to record the fuel pumped into each tank when refilling. It works best by filling to the tank filler neck so that it is a known position. During my initial flights there were some large discrepancies in the fuel burn between the left and right tanks, with the fuel selector in the BOTH position. Over time this discrepancy gradually reduced. The higher fuel burn wasn't always from the same tank and I attributed this to flying for several hours at a speed that was faster or slower than the normal cruise speed (115 KTAS), or to flying many circuits in one direction such that I was allowing the aircraft to become out of balance in one turn direction. Normally it shouldn't make any difference of course.
Reserve Fuel
I always plan to land with at least 40 liters of fuel remaining. This reduces the chance that the fuel lines become unported inadvertently. This gives a range of approximately 4 hours at 115kts (460nm plus reserves).
Some Bearhawks have auxiliary fuel tanks. These are an optional extra available from the kitset manufacturer that hold an additional 80 liters.
Center of Gravity
The Bearhawk is pleasant to fly at a CG forward of 20 inches. Aft of 20 inches it becomes quite sensitive in pitch and more sensitive in yaw. When flying near the aft limit of 22.5" it demands constant attention. At aft CG settings the pitch trim doesn't need much adjustment.
The aircraft is also more sensitive in yaw when landing with an aft CG.
Lean of Peak - Efficiency
As a rule of thumb, I plan on an average of 42 lph to include takeoff, climb and landing.
A higher level cruise results in a higher TAS, whereas a low level cruise results in better efficiency. This is largely because the engine uses a lot more fuel to climb to altitude (particularly if climbing full rich). Therefore all else being equal shorter flights are more efficient at low altitudes and longer flights are more efficient (and faster) at higher altitudes.
A typical full rich/full power fuel burn is 82 lph on the IO540. Lycoming recommend maintaining the mixture full rich until 5000ft, then leaning to maintain a constant EGT.
LOP settings typically result in an additional 100nm per tank of fuel for a 10 - 15 kt reduction in cruise speed. For example when LOP and burning 38 lph at 115 kts the theoretical maximum range (including reserve fuel) from full fuel tanks (205 liters) is over 600nm. However when ROP at 55 lph and 125 kts the maximum range is less than 500nm. That's a significant difference of around a 20% increase in efficiency. In addition the engine runs a lot cleaner and doesn't produce Carbon Monoxide.
Flow matching the injectors
This is a lot simpler than it sounds, and yields results that make it well worth while. It does require having EGT gauges and an engine monitor.
On my Lycoming engine, I performed what's known as a GAMI SPREAD test. Essentially you fly to about 8000ft and very slowly lean the engine until it just starts to falter (or close), repeat it a few times, then download the data. Savvy Aviation offer a free account that analyzes the data, with a GAMI SPREAD function.
It showed that when I moved the mixture to lean of peak (LOP), 5 of the cylinders were operating cooler and lean, but the #1 cylinder was still quite rich and operating near peak EGT. This meant that I wasn't able to run fully lean of peak at low altitudes where the ambient temperature was warmer, or the #1 cylinder would be too hot.
I purchased some smaller restrictors from Airflow Performance, and installed one in the #1 fuel injector. This takes about 3 minutes. The injector remains in place while you undo the top nut, change the restrictor, replace the nut, and go flying.
This now showed the #1 cylinder to now be running leaner and closer to the other cylinders, meaning that they all peak together, and therefore they all sit LOP together. It's now easy for me to run LOP at low (or high) altitudes, for a large fuel saving.
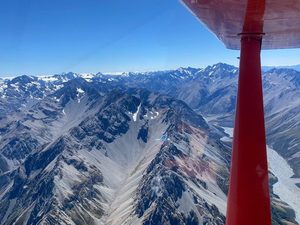
This post is from Neville's Bearhawk