Fuel Tanks Leak Checked
Back in the shop after way too many days off. Pressure checking the tanks took longer than expected. Cure time on the ProSeal took a solid week then other commitments got in the way. I started by installing the sump drain, fuel pickup fitting and the upper plug in each tank using fuel proof thread sealant. I was forced to order it from Amazon due to unavailability locally. Then I hooked up the manometer that I'd previously set up to apply the 1 PSI pressure needed in the tanks. I found out this was a lot easier said than done. Any leaks, no matter how small, quickly caused the manometer to lose pressure and the water columns would even out. You can only add so much water before its completely filled and then you need to disconnect it all, dump the water out and retry. A huge pain. So, I reverted to the balloon and hand pump method which worked much better and was easier to manage and repressurize without taking everything apart. I should've done this method from the start. The learning curve was steep buffered by my awareness to not damage the tanks through over pressurization. I was expecting the balloon to inflate almost immediately as I started applying pressure to the tank with the hand pump. In reality the balloon would slightly pressurize and attain its shape but not expand in size from this initial slightly inflated position even after multiple pumps. Because the balloon wasn't growing in size as I pumped it seemed like I had a sizable leak somewhere, but I couldn't find any with soapy water. I also thought maybe the pump was defective but a quick check on a car tire proved that wrong. Fitting a balloon directly to the pump resulted in immediate inflation and growth of the balloon causing more confusion. Finally, after stroking the air pump multiple times, and hearing the slight creaking of metal as the tank pressurized, the balloon suddenly and quickly inflated to a medium size as air rushed into it. I finally realized the large volume of air in the tank needed to pressurize enough to overcome the natural resistance the rubber in the balloon naturally has and when that point was reached air would suddenly fill the balloon. This inflation is the safety valve that prevents over pressurizing the tank. Best technique was to get the balloon moderately inflated, then disconnect the pump from the Schrader valve as air was lost through the pump when not in use. The balloon would stay inflated with only a slight leak around its neck where it slipped over the AN fitting. I took my time, sprayed soapy water liberally all over every seam and rivet line, and inspected for air leaks, occasionally refilling the balloon as it decreased in size. I was rewarded with no detectable leaks in either tank. And the recently installed fuel senders were fine too. Whew. From there my bride helped me lift a wing on to my table and I got the right tank re-installed, and all fasteners torqued with little difficulty. Hopefully the left tank will go back on as easily.
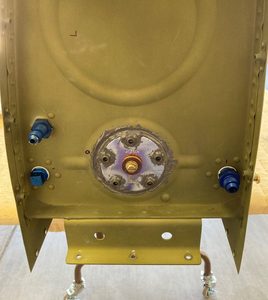
All AN fittings installed with thread sealant. ProSeal around the sender flange took a full week to cure.
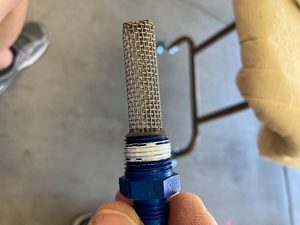
Fuel pickup with built in strainer and thread sealant applied before installation.
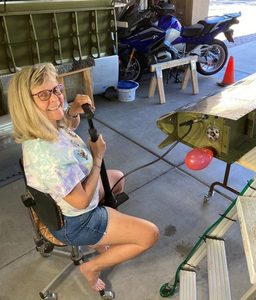
My bride keeping the balloon inflated just enough to keep tank pressurized.
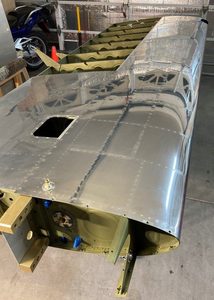
Tank went back on right wing without too much difficulty.
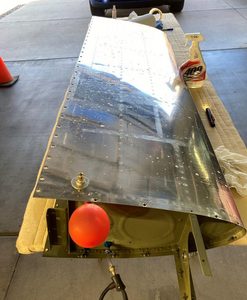
Sprayed soapy water all over looking for leaks, Found none. Yay.
This post is from Scott's RV-14 Build