Getting the Cowling Right
Yes. I haven't posted lately. But that didn't mean I wasn't out in the hanger working. Only that what I had to show for my all my efforts was pretty unexciting. Previously I was faced with the quandary of how to raise the lower edges of the cowling intakes so the rubber seals would fit underneath them properly. I decided to build up the upper side of the lower edges with flox, sand it smooth and contour, then grind away the underlying fiberglass to effectively raise the lower intake edges so the rubber seals would have room to fit correctly. I proceeded to do that and after a lot of sanding and filling achieved that goal. I had to create a variety of rounded small sanding blocks to match the contours of the intakes. I moved on to hand forming the metal strips that are bolted underneath the lower intakes lips that clamp the rubber seals in position. More flox was used to fill gaps under the metal retaining strips and then sanded to shape. I then proceeded to alter the top cowling so the outboard intake edges join up correctly with the lower cowling outboard intake edges. This involved yet more flox and lots more sanding to achieve the desired shape. I'm getting close to installing the rubber seals using the clamping strips and that will be the litmus test of all this work. I'm frankly sick of working on the cowling and baffling ready to move on to something more "fun."

Cured flox sanded to match the cowling edges.
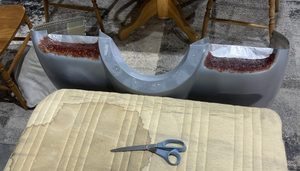
Wet flox layed up on the lower intake lips.
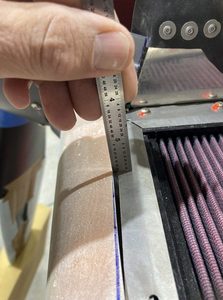
After sanding was complete I had raised the intake lips 5/32" which should allow the seals to fit underneath and lie flush on the intake ramps,
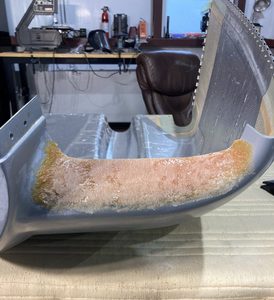
Initial sanding of the dried flox to match the previous intake contour..
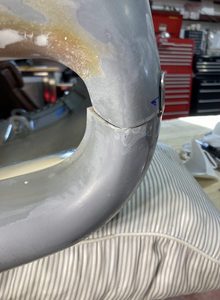
Front of cowling with obvious offset.
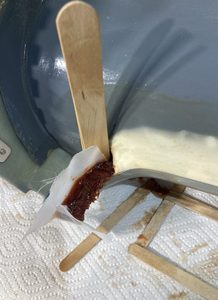
Applying more flox to provide underlying structure when material is sanded away to match the bottom cowling.
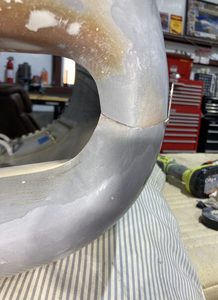
Front after corrective sanding so they match up. Note the amber flox peeking through after sanding away the fiberglass as needed. Got a nice tight seam too. Aesthetically pleasing.
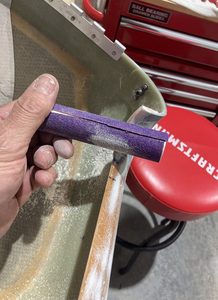
Sandpaper superglued to various PVC pipe sizes made good sanding blocks for curved surfaces.
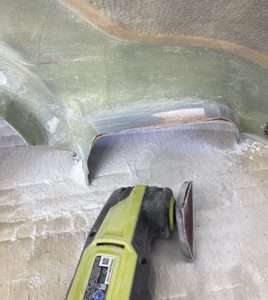
Using 40 grit paper to sand away the underlying fiberglass to make room for the rubber seals.
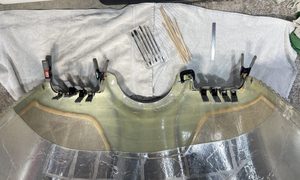
Multiple clamps used to secure the metal seal strips. Flox is used to fill voids and gaps then sanded to contour.
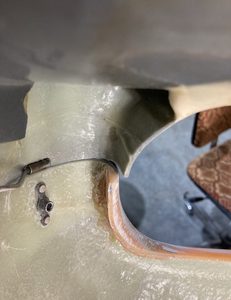
Top and bottom cowling secured to each other, Not the big gap between the 2 edges. Needs to be corrected.
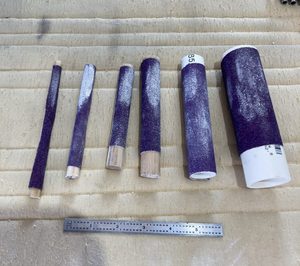
My sanding blocks. I also used popsicles sticks and tongue depressors with sanding paper glued to them to get at tight spots.
This post is from Scott's RV-14 Build