Wingtip Progression
The two wingtips are labor intensive with a lot of trimming, sanding, test fitting, then more trimming and sanding. Messy work.Getting the fit right next to the ailerons and in particular fitting the clear light covers into their recessed mounts is tedious. You really have to ease into the final fit on the light covers bit by bit since it's a complex shape. Adjusting one edge affects the others. Once material is removed it can't be put back. After the wingtips are match drilled and clecoed into position all holes are upsized to #27 then dimpled to accept a #6 screw head. The wingtips are drilled for nutplates (42), all holes are countersunk and nutplates riveted on. The rivets are deliberately underdriven into the relatively soft fiberglass. The left wingtip is nearly done and both clear light covers completed. Now I'm forging ahead on the right wingtip.
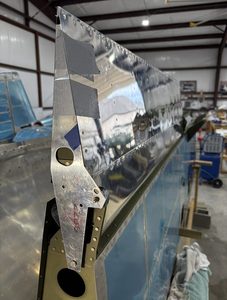
Fixture used to secure the ailerons in the neutral position. The aileron is secured to it with duct tape.
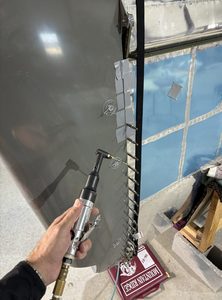
Match drilling the wing skins into the wing tips. Clecoing as drilling progresses.
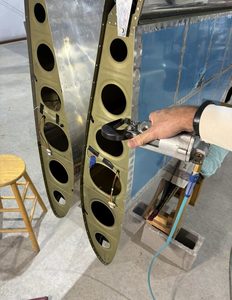
Wing skin holes upsized to #27 then dimpled with the squeezer.
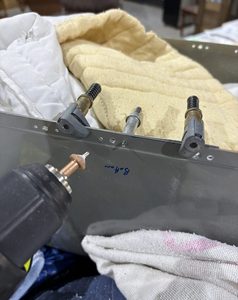
Countersinking the rivers holes. I created a metal backing plate so the countersink tool wouldn't wander in the fiberglass.
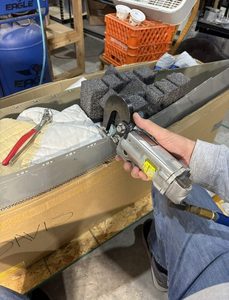
Riveting on all the nutplates with the squeezer. Securing the somewhat flimsy, flexible wing tip for riveting proved challenging. Put wingtip in a large box then stuffed it with rags and foam to make it more rigid.
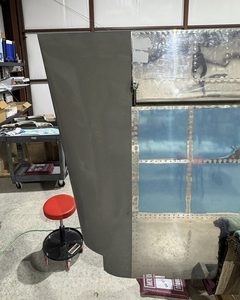
Left wingtip screwed to wing. Good fit and a nice tight aileron gap.
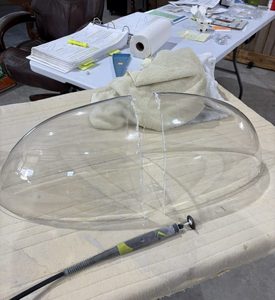
For the light covers you need cut this big piece in half first to make 2 blanks.
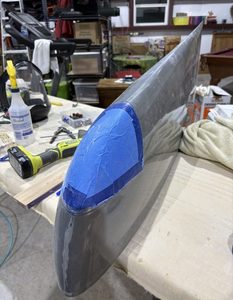
Blue tape in/out to prevent scratches. Edges are progressively trimmed then sanded to fit the recess in the wing tip.
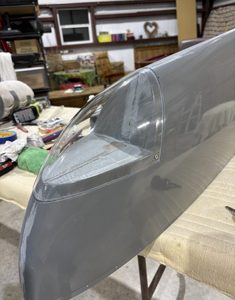
Final cover fitment held on with screws.
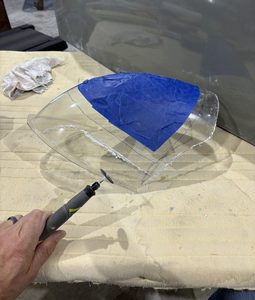
More rough trimming of the light cover.
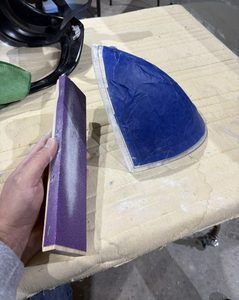
Tweaking with a sanding block for nice straight edges.