Custom fuel tank skins match drill holes to main spar
Sling provided customised fuel tank skins with the front spar flange holes omitted, both top and bottom. As found in previous investigations, the error in the fold of the front facing flanges of the main spar (the top one in particular) was sufficient (>2mm in places) as to make upsizing to 4.8mm rivets impractical (and hole elongation very undesirable). By shifting the fuel tans skins a little it would have been possible to mitigate this to some degree, but still the upsizing (including the Avinox stainless steel rivets, which I in fact sourced) would have been required. The inner spar layer clearance holes would have also had to be enlarged. The result after all this work would have been a slightly distorted wing surface profile, and additional shims would have been required on many of the wing mounting brackets. In the event Sling provided customised skins with these holes missing, which I would match drill to the actual main spar hole positions - thus avoiding all this complication.
The fuel tank back channels and mounts were assembled with clecoes and bolted into place. Checks were made to ensure the mounts were fully in contact with the spar surface and not caught up on the L-section strength members.
The original fuel tank skins were laid over the new skins, and with the help of the doublers, the original mismatches were re-confirmed. This also help to verify the fuel tanks were indeed properly bedded down.
The job was done with the 4mm strap doubler. I learned immediately that this would not give a good result just be using it to guide a #20 drill. The strap doubler would be shifted about and distorted by the various lateral stresses from the drill action leading to a poor result. Using a cleco clamp (specially altered) to constrain a slight twisting mode of the doubler did not help much either. Only be keeping the doubler fully unloded could I achieve fairly reliable alignment. Initially I made a mark hand twirling a #20 drill bit. This mark was then used to guide a centre punch, which in turn guided a 1/16" drill hole. This was chuck reamed to 2.5mm and a visual inspection of the alignment made. Chuck reaming then to 3.3mm was then done and a further check of alignment made. At each of these stages any needed corrections were made with a needle file. Finally the chuck reamer was used to guide hand application of a 4.1 chuck reamer, ensuring no significant lateral forces were applied to the strap doubler. After initial cutting the reamer guided itself anyway. Most holes were perfectly aligned, with errors of 0.1 to 0.2mm at most.
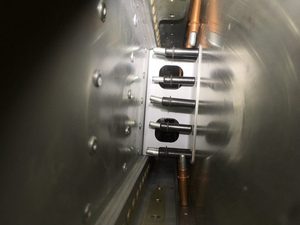
Check for proper bedding down of fuel tank brackets
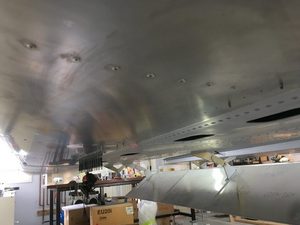
Prior to match drilling bottom holes
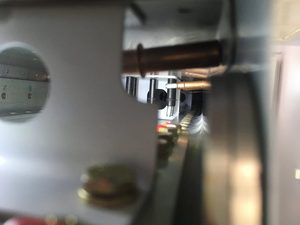
Check for proper bedding down of fuel tank brackets
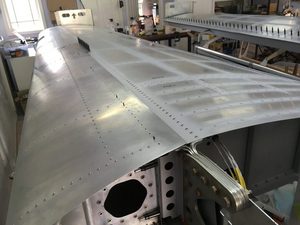
Prior to match drilling top holes
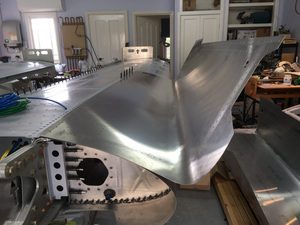
Example of original fuel tank skin laid back-to-back and used to mark the nominal position of holes on the custom skin
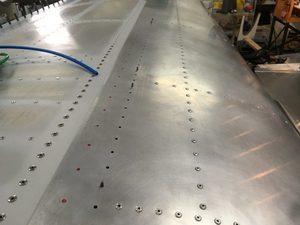
Example of marked positions of where the main spar holes should be
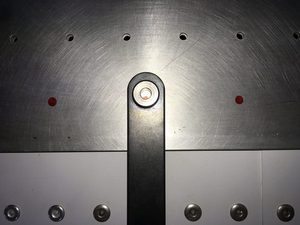
An example of the mismatch - the strap doubler shows where the main spar holes actually are.
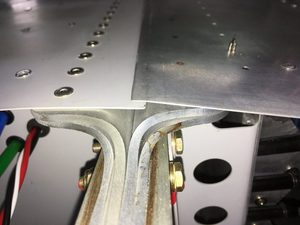
A sanity check - this is the degree of skin overlap that should occur and which will be achieved, confirming the wing shape is correct (left skin)
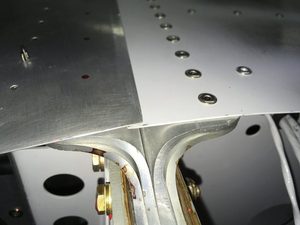
And the same for the right skin
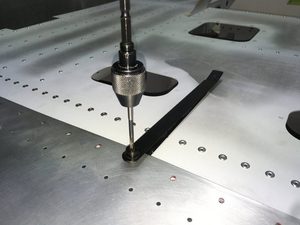
Final step on hole formation - the 4.1mm chuck reamer
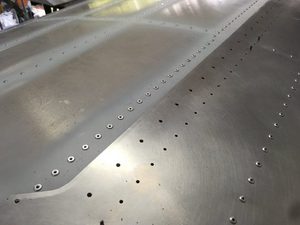
Final result - top side, right. Errors of up to 2mm were present (slight greater still for the left wing) and in fact decreased at each end of the flange
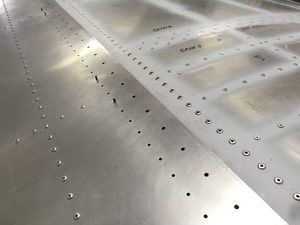
Another view
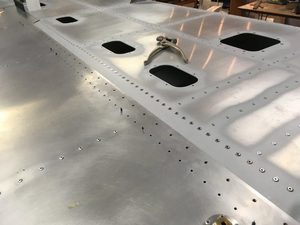
Final result - bottom side, right. The spar hole errors were generally smaller on the bottom side.
This post is from Adam Dickson