11 May 2024
Short elevator torque tube and front to rear join
Fitted eyebolt for autopilot to the short elevator torque tube and torqued to 2.5nm, applied torque seal. The other eyebolts were fitted previously. Lightly ground the inside of the two outer Vesconite bushings to achieve smooth rotation of the torque tube. Riveted the torque tube in place. Riveted the rear seat support channel and back seat strengthening channel in place. Result was not acceptable, so I de-riveted everything again including the autopilot bellcrank on the torque tube (stainless steel rivets, which needed a drill press to remove them carefully), removed the center Vesconite bush and replaced it with one previously lightly ground inside, then test fitted again after applying the old unground center bushing to the pilot's side end of the torque tube. Far better, but a little grinding was still required for the end bushing. Fitted the three lock bushings to the short torque tube, drilled and riveted in place with 4.0mm rivets. Complies with service bulletin 0021. Installed new stainless steel rivets for the autopilot bellcrank. Reinstalled the elevator torque tube.
Gotcha: the rear floor skin should really go on after the torque tube is riveted in place, there is almost no way to access the one center rear rivet for the bushing retainer bracket other than from underneath. However, the skin is required in order to get proper alignment of the ribs which support the torque tube, otherwise it locks up. It's a really poor design and really difficult to get right, Sling needs to re-think their approach or provide some form of tool to enable access to the rivets, it's impossible to get a rivet gun into the confined space. I made a small angle tool which only just fitted - it worked, but was exceedingly difficult to do. The outer brackets can be accessed without too much issue and are the primary support brackets.
I'm still not happy with this and will probably remove and redo the installation in future.
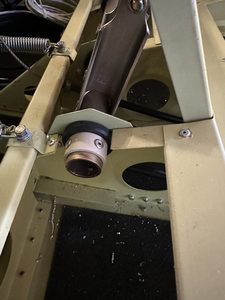
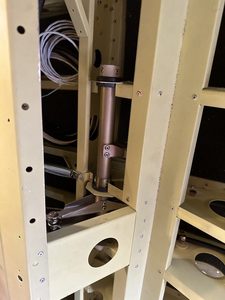