17 & 24 Aug 2024
Elevator short torque tube - again
The elevator short torque tube... the bane of other Sling builders' existence and mine too. The design with the Vesconite bushings is really poor and causes the torque tube assembly to lock up if there is even the slightest misalignment. That worries me, because small movements in the fuselage assembly could cause it to lock at the worst possible time. I'm on torque tube assembly number three now, so I decided to do what some other builders have done and install bearings instead. This was a time consuming but worthwhile process and replaces the installation I completed in May 2024 but was not happy with.
I ordered some 1" ID flanged ball bearings (1 1/4" OD, 1/4" Thickness) i.e. very thin section, with ID to match the OD of the torque tube, from Servo City in the USA (SKU 1601-0001-1000) along with some 1.00" shafting and tubing spacers (SKU 633116) and aluminium clamping collars (1" Bore) (SKU 2910-0001-1000). I also created a very simple design in LibreCAD with a 4.5"x4.5" square of 6061-T6 1mm aluminium (same material as the original CF-BKT-005 brackets) with a hole in the centre - one an exact size to match the bearing OD 1.245" (used the bearing STEP file to get the specs) and two other versions - very slightly undersized hole and the same in oversize to use as templates. Send Cut Send in the USA supplied this material.
I attempted to fit the bearings to the third torque tube, but the tube was slightly oversized and the bearings damaged the tube, so I reverted to tube number 2. After carefully drilling out the stainless steel rivets in the autopilot bellcrank to permit removal of the centre Vesconite bushing, the bearings were fitted without any hassle. Bearings were greased with white lithium-based grease as recommended by Servo City (I used a syringe to force it into the races, worked well), in this case some Herschell heavy duty garage door and gate grease. The torque tube rotates through a very limited range.
I then manufactured a few templates for the bearing brackets using the material from Send Cut Send and settled on a design which worked well. The template provides 4 holes for attachment to the ribs, so these were drilled to match the original ribs and Sling brackets with two additional holes on the lower side to provide extra stability. The material with the exact size hole was an excellent match for the bearings, requiring press fitment but not excessive force. The brackets were primered for protection against corrosion. I also drilled out the two rivets in the RF-BKT-013 left and right at the top where they overlap the ribs in the forward fuselage. This allowed the ribs to take on a better neutral position - in hindsight I should only have riveted them after installing the first torque tube. Anyway, one learns as you go - they were riveted again once everything was installed.
After deburring the newly drilled holes and multiple test fits to get the torque tube nicely centered in the console, the autopilot bellcrank was re-riveted in place with stainless steel rivets and then the whole assembly was bolted in position using M4 x 12 mm stainless steel button head screws and nylock nuts. Sling recommended M5 sizing if using 2 in place of the original 4mm rivets, but I'm using 4 of them so M4 should suffice. I decided against rivets after experiencing the removal of the first torque tube, which was almost impossible.
The assembly includes spacers between the bearings and clamping collars. The bearings were orientated with the clamping collars on the outside of the centre channel to prevent interference with the rudder cables. A very small amount of material was removed from the top rear of the floor ribs to provide clearance for the collars. The bolts in the clamping collars were secured with Loctite 243, and torque seal applied to the other nuts. The backseat strengthening channel and rear seat support channel were then reinstalled and riveted in place.
The result is exceptionally smooth, an excellent outcome.
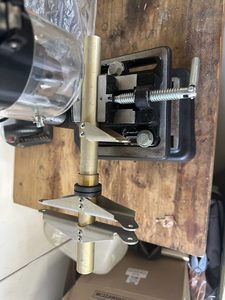
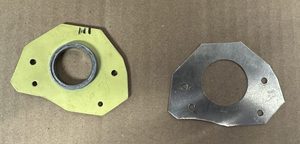
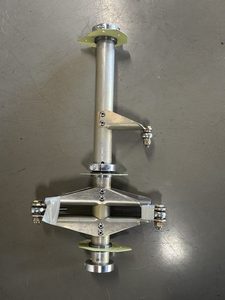
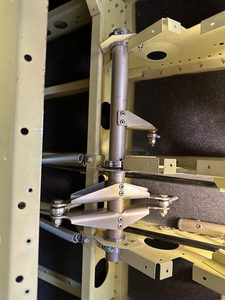
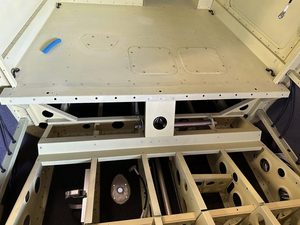
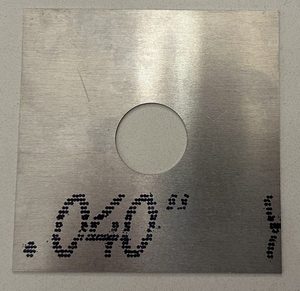