Got The Engine Hung
A big day for any build is getting the engine mounted. For mine to happen several other tasks were accomplished over the past few days. I first installed the sensor block mounted to the left upper firewall. This block holds the oil and fuel pressure sensors and the manifold pressure sensor. I broke with the plans in putting the manifold pressure sensor there. Normally its mounted by itself on the upper right firewall. But since I'm running dual PMags I went with the Aircraft Specialty PMag setup and their hoses have the MP sensor on the left side. I think it makes for a cleaner install. Various fittings were installed and clocked properly on the aft engine accessory case. Oil temp and pressure, oil cooler inlet and outlet fittings, various fuel pump fittings and the manifold pressure pickup among others. It's much easier to install them now then later. Hopefully none of them leak. Being NPT fitting they must be quite tight to seal, but not so tight that you damage threads. When clocking to a certain position you have to use judgment when reaching that certain clock position if the fitting is tight enough or warrants another full revolution to the same clock position. The prop governor is also test fitted, its bracket fabricated, adjusted then re-installed later. I needed four lock washers for this. Aircraft Spruce sells generic AN lock washers of the type needed for .05 each. The actual Lycoming part number/lock washers are $1.99/each. Being Experimental you could legally install ACE Hardware lock washers, but I went with the Lycoming ones. But honestly, $8.00 for four lock washers!? My build buddy Craig suggested I fill and bleed the brakes prior to mounting the engine. Good idea. Using a large clear plastic syringe and clear plastic tubing, I injected the appropriate Mil-Spec fluid through the bleed port in each caliper. This more effectively removes air in the lines. Since all the interior brake lines are translucent plastic it's easy to spot air bubbles. We discovered a leak at the firewall on the front side due to a bad flare with a miniscule crack. Fortunately, we were able to cut off the bad flare, reflare the end and reconnect which stopped the leak. And I was able to salvage the entire left brake line instead of fabricating a new one. Finally, it was time to hang the engine. For something that everyone needs to do there isn't a lot of detailed info floating around on best practices. Lycoming offers no guidance that I could find. I came across a good article taken from the VAF Forum which detailed techniques with accompanying photos. The four mounting bolts that go through the aft engine case are not parallel to each other. That coupled with the hard rubber elastomeric bushings with their accompanying spacers and washers makes the 3rd and 4th lower bolts challenging. Fortunately, my buddy Craig had done this before, I'd done my homework and we were organized. I moved the fuselage so it was half sticking out my garage door (with the electric opener unplugged!) so the engine lift could face the motor mount head on and we had room to maneuver. Once initially positioned with the hoist, we got the first two upper bolts and nuts in. Then used the nuts to draw the engine closer to the mount which facilitated getting the two lower bolts and bushings installed. All told from start it finish it only took 25 minutes to get all 4 bolts in place and the nuts on. Being thick AN7 bolts they get torqued to a beefy 450-500 in/lbs. You have to turn the bolts and not the nut. Using a beam torque wrench I found the drag torque was 75 in/lb alone which was added to the torque needed. All told about 550 in/lbs or 45 ft/lbs on the click type torque wrench was used for final torque. After that we stood back and admired our work. I must admit it looked cool to see the engine hanging there and it was a satisfying moment.
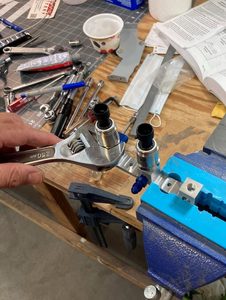
Mounting the fuel and oil pressure sensors on the sensor block that mounts to the firewall.
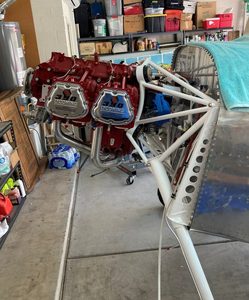
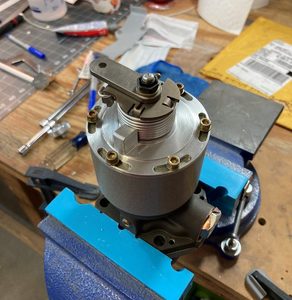
The oil-controlled propeller governor that's mounted on the front left engine pad.
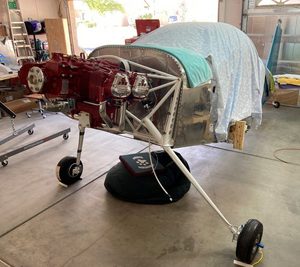
Very satisfying to see the engine finally in place.
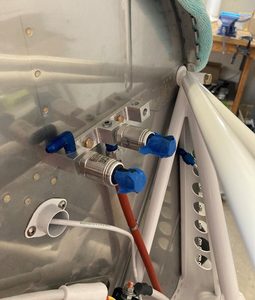
Sensor block mounted. The third lug will contain the manifold pressure sensor in a break with the plans. Using the Aircraft Specialty PMag hose setup.
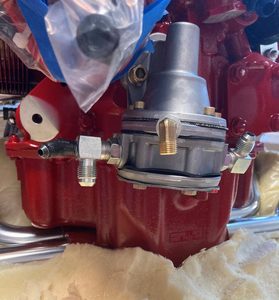
Various fitting are installed and clocked on the rear accessory case prior to hanging the engine due to easier access. Here are 3 fittings mounted on the fuel pump. All are clocked differently,
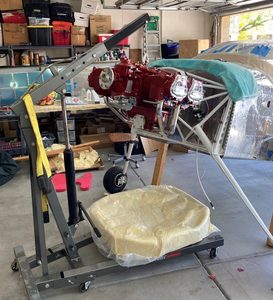
Getting the engine positioned with a hoist. Two people are a must for this process.
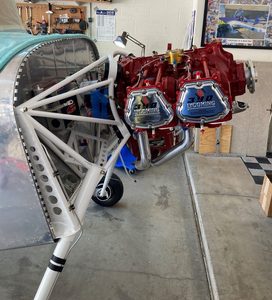